What are the three most common electrical problems in an electric motor?
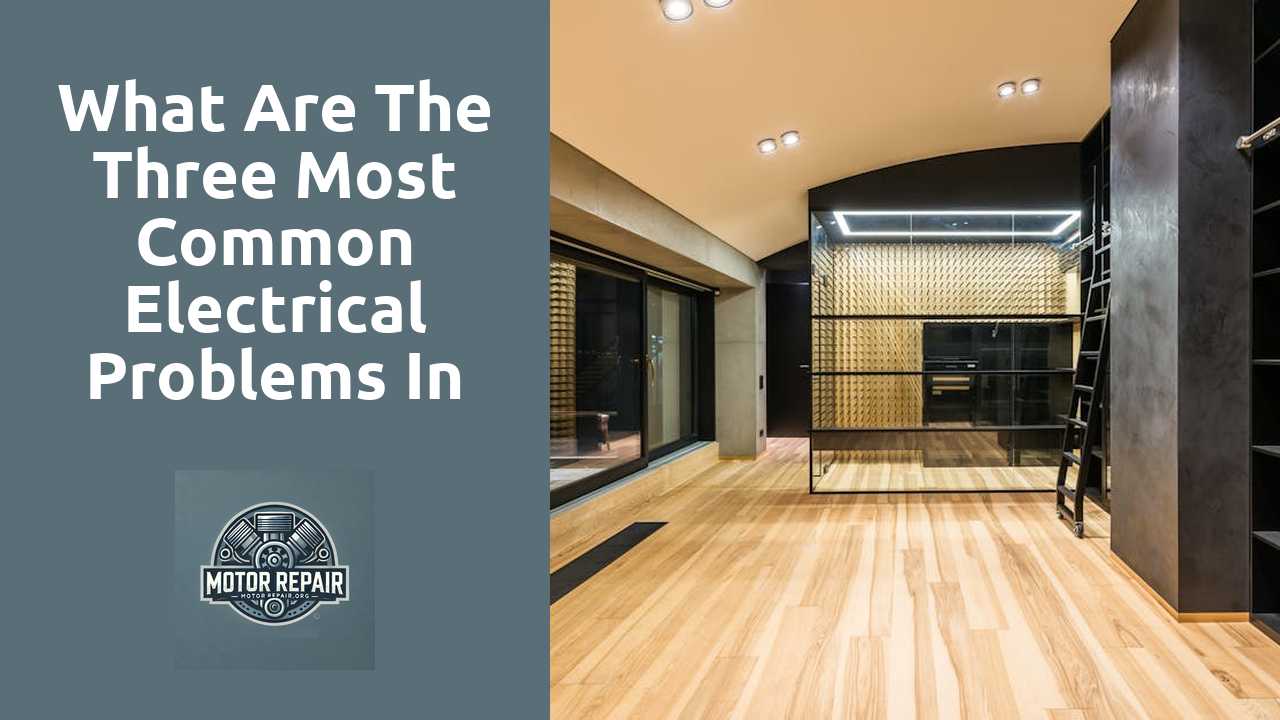
Table Of Contents
Voltage Fluctuations
Electrical systems can experience issues due to fluctuations in voltage, which may arise from various factors such as power supply variations, equipment malfunction, or external disturbances in the grid. Motors operating under inconsistent voltage conditions may struggle to perform efficiently, often resulting in overheating or stalling. The machinery bears the risk of damage since it can lead to increased wear and potentially shorten its lifespan.
Inconsistent voltage levels can disrupt the motor's operational efficiency, leading to performance declines and potential system failures. These fluctuations can also cause the motor to draw excessive current, further exacerbating issues like overheating. It becomes crucial for facility operators to monitor voltage supply carefully and employ voltage regulation mechanisms to ensure that electric motors operate within their specified limits.
See here for more great tips.
Consequences of Inconsistent Voltage Supply
Inconsistent voltage supply can lead to a range of operational issues within an electric motor. Fluctuations can cause the motor to run inefficiently, leading to an increase in energy consumption and potentially higher utility bills. The frequent oscillation in voltage levels places additional stress on the motor components, which can contribute to premature wear and a decrease in the overall lifespan of the equipment.
Over time, this instability can trigger various protective mechanisms in the motor, such as tripping circuits or overheating. Such responses not only disrupt regular functioning but also necessitate frequent maintenance interventions, further increasing operational downtime. Ultimately, these consequences can compromise productivity and escalate repair costs, making it imperative to address voltage stability to ensure optimal motor performance.
Motor Contamination
Contaminants such as dust, dirt, and moisture can significantly impair the performance of electric motors. These foreign materials often infiltrate the motor housing, leading to insulation breakdown and increased wear on components. Over time, this contamination can result in overheating and eventual motor failure. Regular maintenance and cleaning are essential to prevent these issues and ensure that motors operate efficiently and reliably.
In industrial settings, the presence of lubricants and chemicals can further exacerbate contamination problems. These substances can degrade insulation materials and struggle to provide adequate cooling. Prompt identification and remediation of contamination sources are critical to maintaining motor longevity. Implementing proper filtration systems and regular inspections can help mitigate the risks associated with motor contamination, ultimately protecting the investment in electric motor systems.
Effects of Dust and Debris on Motor Functionality
Dust and debris can significantly impair the functionality of electric motors, leading to reduced efficiency and potential failure. Particles that accumulate inside the motor housing can obstruct ventilation pathways, causing overheating due to inadequate cooling. This elevated temperature can degrade insulation on windings, increasing the risk of electrical shorts and eventual motor burnout.
Additionally, contaminants can interfere with moving components, increasing friction and wear. This friction can lead to increased energy consumption, as the motor works harder to maintain performance levels. In more severe cases, dirt can cause bearings to seize, leading to complete motor breakdown, resulting in costly repairs and downtime. Regular maintenance and cleaning are essential to prevent these issues and ensure optimal motor performance.
Mechanical Misalignment
Mechanical misalignment occurs when the motor's rotor and stator are not properly aligned, leading to a range of operational issues. This misalignment can stem from improper installation, wear and tear, or shifting in the base or foundation of the motor. When misalignment takes place, it can cause excessive vibrations during operation, increasing the wear on bearings and other moving parts. This not only reduces the efficiency of the motor but also shortens its lifespan, ultimately leading to increased maintenance costs and potential downtime.
Detecting misalignment early is crucial to maintaining optimal motor performance. Common signs include unusual noises, increased vibration levels, and overheating. Operators may notice that the motor struggles to reach its normal operating speed or produces inconsistent power. Addressing misalignment promptly through realignment or repair can significantly enhance the motor's operational reliability and efficiency, preventing more extensive damage or failure in the future.
Signs of Misalignment and Its Implications
Misalignment in electric motors can manifest through several distinct signs. One of the most noticeable indicators is an increase in vibration levels. A properly aligned motor operates smoothly, while a misaligned motor often causes excessive vibration that can be felt and measured. This abnormal movement can lead to accelerated wear on bearings and other components, ultimately affecting the motor's efficiency and lifespan.
Another significant symptom of misalignment is unusual noise production. When a motor is misaligned, it may produce grinding, rattling, or thumping sounds that deviate from its normal operating noise. These sounds indicate that internal parts are not working together as they should, which can result in further mechanical issues if left unaddressed. Promptly recognizing these signs allows for timely maintenance, helping to prevent extensive damage and costly repairs.
FAQS
What are voltage fluctuations and how do they affect electric motors?
Voltage fluctuations refer to variations in the electrical supply that can lead to inconsistent performance in electric motors. These fluctuations can cause overheating, increased wear and tear, and ultimately shorten the motor's lifespan.
How can I identify if my electric motor is contaminated?
Signs of motor contamination include unusual noises, overheating, decreased performance, and visible dust or debris on the motor components. Regular maintenance checks can help in identifying contamination early.
What can cause mechanical misalignment in electric motors?
Mechanical misalignment can be caused by factors such as improper installation, wear and tear over time, or external forces affecting the motor's positioning. Regular inspections can help catch misalignment issues before they escalate.
What are the consequences of motor contamination?
Motor contamination can lead to overheating, reduced efficiency, increased energy consumption, and potential motor failure. Keeping the motor clean and free of debris is essential for optimal operation.
How often should electric motors be inspected for these common problems?
It is advisable to inspect electric motors regularly, typically every 3 to 6 months, depending on the operating environment and usage. More frequent inspections may be needed in dusty or high-wear conditions.
Related Links
electric motor repairHow to troubleshoot an electric motor?
Is it worth repairing an electric motor?
Can a small electric motor be repaired?