Expert Guide to Generator Motor Repair and Efficient Generator Repair Services
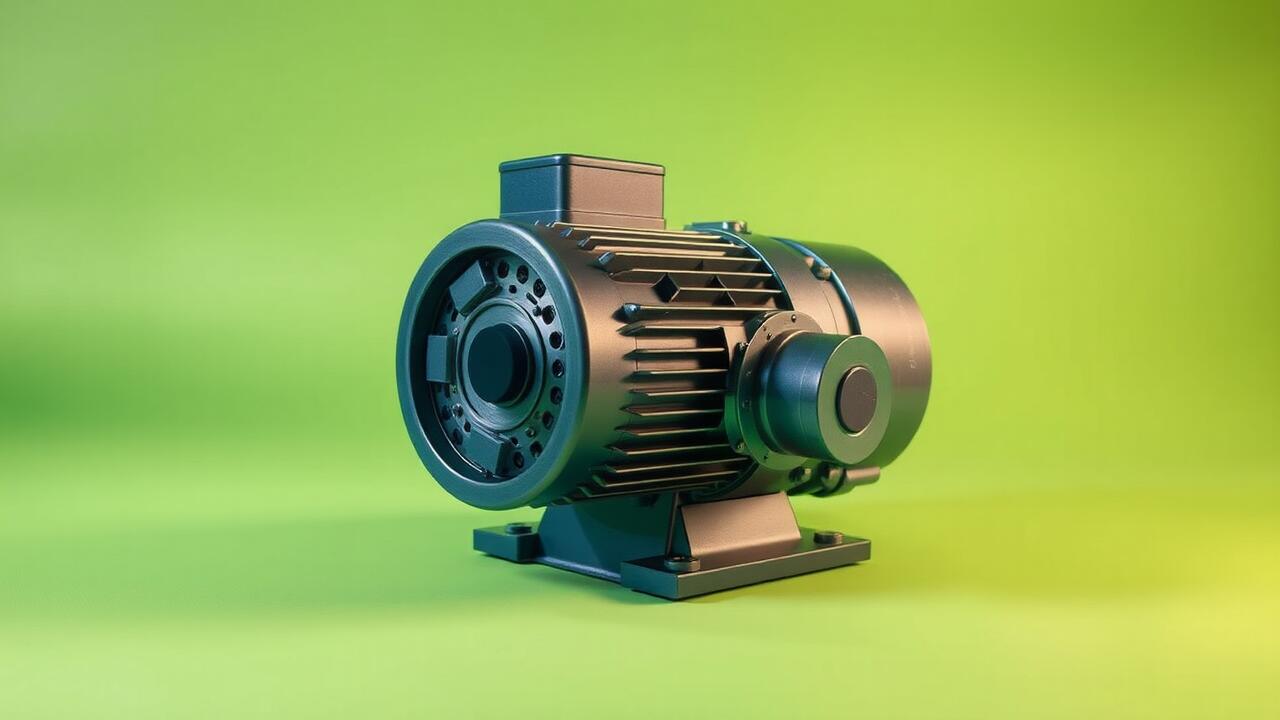
Table Of Contents
Key Takeaways
- Comprehending generator motor restoration processes
- Procedures required for generator maintenance
- Methods for electrical motor restoration
- Instruments and apparatus needed for repairs
- Diagnosing frequent issues
- Expert versus do-it-yourself repair choices
Understanding Generator Motor Repair
Regular generator motor repair is essential to maintain the efficiency and longevity of both AC and DC electric motors. Routine inspections can help identify potential issues before they escalate, ensuring that the power generator operates smoothly. Common problems range from electrical failures in the motor to mechanical wear and tear. Understanding the intricacies of electric motors, including troubleshooting techniques for generators, can save time and costs associated with unexpected breakdowns. Ultimately, proper maintenance of generator motors not only enhances performance but also maximizes the reliability of both DC motors and their AC counterparts.
Importance of Regular Maintenance
Regular maintenance plays a crucial role in ensuring the longevity and efficiency of generator motor repair. Neglecting routine checks can lead to severe issues, especially in power generators and backup generators. For instance, improper maintenance of DC electric motors can result in overheating and premature failure. Regular inspections can help identify potential problems early, allowing for timely repairs and avoiding more extensive damage to the machine.
Maintaining fractional horsepower motors is equally important, as these small machines are often integral to larger electrical systems. A well-maintained motor not only performs better but also reduces energy consumption. Regular servicing can enhance the reliability of generators, ensuring they function optimally during critical times. Effective generator motor repair minimizes downtime and prolongs the lifespan of motors, making maintenance a vital aspect of ownership.
Common Issues with Generator Motors
Generator motors can experience a variety of issues that necessitate prompt attention to ensure optimal performance. One common problem is a drop in voltage output, which may stem from worn or damaged rotor components. Regular repair and maintenance are crucial to identify these faults early on. Neglecting these issues can lead to extensive repairs, especially if the turbines or other integral machinery parts are affected.
Another frequent issue involves the overheating of generator motors, often due to inadequate lubrication or bearing failures. This can result in irreversible damage to the machinery if not addressed swiftly. Technicians may need to reverse engineer certain components during the repair process to restore proper functionality. Conducting routine checks can help prevent these complications and extend the lifespan of the generator motor through effective repairs.
Steps Involved in Generator Repair
Generator motor repair requires a systematic approach that begins with diagnosing electrical problems. Techniques such as vibration analysis help identify issues related to the engine's performance and potential failures in high-voltage systems. Inspecting components like field coils is essential for assessing the integrity of electrical insulation. For more complex repairs, collaborating with a machine shop may be necessary, particularly when the repairs involve specialized equipment from the original equipment manufacturer. Addressing these concerns efficiently can significantly reduce maintenance costs and prolong the lifespan of the generator motor, ensuring it operates smoothly, even in demanding conditions like those faced by four-wheel drive vehicles.
Diagnosing Electrical Problems
Identifying electrical problems in generator motors is crucial for effective generator motor repair. Problems can stem from various components, including the windings, batteries, or even connections that have come loose. To troubleshoot, inspect each part for signs of wear or damage. A common issue might be vibrations that occur during operation, indicating a misalignment or imbalance. These factors can directly affect the horsepower and overall performance of the generator motor.
Sometimes, electrical issues may arise from welding faults or shorts within the system. Proper maintenance practices include regularly checking the circuitry and ensuring connections are secure. It is also essential to consider the fuel supply, as inadequate fuel can lead to electrical failures. A thorough diagnostic process can prevent more significant problems down the line and ensure your generator remains fully operational.
Mechanical Repairs and Replacements
Mechanical issues often arise in generator motors due to wear and tear over time. Identifying these problems is essential for effective generator motor repair. Typical repairs may include replacing worn bearings, fixing misalignment, or addressing issues with the rotor or stator. Comprehensive generator repair can restore functionality and extend the lifespan of the equipment, whether it involves full motor/generator replacements or small motor repairs.
Timely mechanical repairs ensure that both commercial and industrial generator repair needs are met efficiently. A thorough assessment of the components can reveal necessary replacements, minimizing downtime. Understanding the intricacies of generator repairs introduction can aid technicians in performing effective maintenance. Expert knowledge of generator motor repair procedures can help to prevent recurring mechanical issues and promote the reliability of the motor/generator systems.
Electric Motor Repair Techniques
Effective electric motor repair techniques are crucial for maintaining the functionality and longevity of both generator motors and electric motors. Skilled technicians understand the intricacies of how electric motors are built, which aids in diagnosing issues related to electric motor parts. This knowledge is essential for conducting in-shop generator repair tasks as well as in-house motor repair services. Small motor repair often requires specialized approaches to ensure that the unique electric motor capabilities are restored. A successful motor repair business relies on a comprehensive understanding of electrical motor products and the specific needs of each motor type. Implementing these techniques can help maximize performance and prevent future breakdowns in generator motor repair and electric motor maintenance.
Inspecting and Testing Electric Motors
Thorough inspection and testing of electric motors are crucial steps in effective generator motor repair. Understanding the condition of generator components helps in identifying potential issues before they escalate. Regular commercial generator maintenance allows for the evaluation of initial motor efficiency, ensuring that the system operates at optimal performance levels. Engaging motor repair specialists can provide valuable insights into necessary repairs or replacements that enhance the longevity of both the motor and the generator.
Complete generator reconditioning often involves precise testing techniques to assess the performance of a motor. Utilizing specialized equipment, technicians can analyze factors such as voltage levels, winding resistance, and insulation integrity. This attention to detail is especially important in industrial and commercial generator maintenance, where reliability is paramount. Addressing any detected deficiencies early on can prevent costly breakdowns and extend the life of a new motor significantly.
Techniques for Motor Rewinding
Rewinding is a critical process in generator motor repair, specifically for addressing issues with generator windings. This technique involves removing the old windings from an AC/DC motor and replacing them with new wire of the appropriate gauge. A proper generator inspection must be conducted to determine the state of the windings and other motor components. Efficient rewinding directly impacts the performance of the generator, ensuring reliable power supply for various industrial applications.
Techniques for motor rewinding require expertise in handling AC/DC motor parts and understanding their functions within generators. Skilled technicians perform mechanical repairs during the rewinding process, ensuring that all components are properly aligned and functioning efficiently. Generator support is vital, as improper handling during rewinding can result in further damage. Regular generator inspections can help identify issues early, allowing timely intervention and prolonging the life of the generator.
Tools and Equipment for Repairs
Proper tools and equipment are crucial for effective generator motor repair, whether addressing AC/DC motors or large power generators. Understanding motor dimensions and specifications ensures that technicians can select the right equipment for both commercial generator and industrial power generator applications. Essential tools include multimeters for electrical diagnostics, wrenches for mechanical adjustments, and specialized instruments for inspecting two-pole generators. Having the right tools simplifies the repair process, whether working on new motors or troubleshooting existing generators. With the appropriate power equipment, technicians can efficiently identify and resolve issues, ensuring optimal performance and longevity of the power equipment.
Essential Tools for Generator Repair
A comprehensive toolkit is crucial for effective generator motor repair. Essential tools include multimeters for electrical testing and wrenches for tightening loose components. Proper inspection of electrical equipment condition ensures that any underlying issues are identified before they lead to more significant problems. Regular maintenance power enhances the life of industrial power generators, allowing them to perform optimally. Skilled technicians can utilize these tools to diagnose issues quickly, ensuring that motors run smoothly and efficiently.
Safety measures must also be part of the essential toolkit for generator services. Personal protective equipment, such as gloves and goggles, safeguards technicians from potential hazards during repairs. Without appropriate safety gear, the risk associated with repairing electrical rotating equipment increases significantly. For legacy motors and top-notch motor repairs, investing in quality tools can make a substantial difference in the outcome of the generator motor repair process. Adopting the right safety practices leads to a more successful and secure working environment.
Safety Equipment for Electric Motor Repair
Proper safety equipment is crucial during generator motor repair to prevent accidents and injuries. Workers should wear insulated gloves and safety goggles to protect against electrical hazards, particularly when working with slow-speed generators and cat® generator sets. Hard hats and steel-toed boots are essential for protection against falling objects and heavy mechanical components. This equipment not only ensures safety during routine maintenance but also during complex tasks such as complete engine rebuilds and turbine component inspection.
Using the right safety gear also enhances the effectiveness of electronic repair services. Having an adequate first aid kit on site is essential for emergencies. For those involved in elevator motor services or dealing with rental generators, adherence to safety protocols is paramount. Proper ear protection should be considered too, especially since high noise levels can occur during generator operation. Ensuring a safe working environment contributes to efficient generator run time and minimizes the risk of accidents during repairs.
- Regularly inspect safety equipment for wear and tear to ensure effectiveness.
- Use lockout/tagout procedures to prevent accidental machine activation during repairs.
- Maintain a clean and organized workspace to reduce tripping hazards.
- Provide training on emergency procedures, including first aid and evacuation plans.
- Ensure proper ventilation in enclosed spaces to prevent inhalation of harmful fumes.
- Encourage workers to report unsafe conditions or equipment malfunctions immediately.
- Use tools with insulated handles to minimize electrical risks during repairs.
Troubleshooting Common Problems
Effective troubleshooting of common issues is crucial for successful generator motor repair. For instance, consistent voltage generation can be disrupted by problems in the electrical system, which necessitates thorough rotor bar inspection and mechanical measuring techniques. Engine manufacturers often recommend specific maintenance protocols to ensure base-mounted motors operate efficiently. Compiling a detailed repair project is essential for diagnosing these issues, as a complete machine overview provides insight into potential failures. Understanding the nuances of a turbine guide can also enhance the repair process, ensuring that generator motor repair is carried out with precision and longevity in mind.
Generator Not Starting Issues
Generator motors that fail to start can stem from a variety of issues. Often, problems with fuel supply or electrical components lead to this situation. A thorough generator motor repair begins with complete fuel management to ensure that the fuel system is functioning properly. Issues with coils or the ignition system can also prevent the generator from initiating the startup process. Electrical testing can pinpoint deficiencies in the wiring or components, allowing technicians to proceed with expert repairs and avoid serious engine damage.
Problems with the power system, including battery failure or starter motor defects, can hinder generator operation. Performing on-site engine re-builds may be necessary in some cases, especially if mechanical issues are detected during diagnostics. Regular inspection and troubleshooting by trained professionals can help identify these issues before they escalate, ensuring a more reliable performance from your generator motor. Addressing generator not starting issues promptly is crucial for maintaining the efficiency and longevity of your power system.
Overheating Issues in Electric Motors
Excessive heat in electric motors can lead to critical failures if not addressed promptly. Common causes include issues within the fuel system, which can affect the overall efficiency of the motor. Implementing regular industrial breaker maintenance is essential to keep the equipment running smoothly. Monitoring the condition of low-voltage units and ensuring proper ventilation in the repair space can help mitigate overheating risks. Neglecting these aspects may result in costly repairs and downtime for the generator motor repair process.
Understanding the significance of proper fueling and maintenance is crucial for optimal performance. Fuel polishing is an effective method to maintain clean fuel, thereby reducing the likelihood of overheating. Regular checks on wheel drive service components can also assist in identifying potential issues before they escalate. By addressing overheating proactively, operators can extend the lifespan of their electric motors and avoid disruptive failures during operation. Proper maintenance techniques can ensure that all parts function harmoniously, enhancing the reliability of the overall system.
Professional vs. DIY Repair Options
Choosing between professional and DIY repair options for generator motor repair involves careful consideration of various factors, especially when addressing power systems concerns. Professionals in repair departments have access to specialized tools and knowledge, making them adept at handling complex issues such as stator windings or vibration issues in biogas turbines. Utilizing an in-shop repair center can enhance efficiency, especially for services like fuel management and fuel deliveries, which are crucial for optimal generator performance. DIY maintenance tips may be suitable for minor fixes, but understanding the limitations of personal expertise is vital to avoid exacerbating problems. Engaging experts ensures thorough evaluation and resolution of issues, preserving the longevity of generator motors.
When to Seek Professional Help
Professional assistance is critical in generator motor repair, especially when facing complex issues that threaten the operating efficiency of the equipment. For instance, vibration problems can indicate deeper mechanical failures or misalignments that require expert evaluation. If you're dealing with high-voltage bushing change-outs or intricate components like wicket gates, experienced technicians with access to a full machine shop are invaluable. Ensuring proper electrical insulation testing and maintenance activities is vital, and professionals are adept at identifying potential hazards that untrained individuals might overlook.
DIY repairs might seem appealing; however, certain situations necessitate professional intervention. Issues such as a generator motor that fails to provide temporary power may stem from complicated electrical faults or components needing thorough inspection. These scenarios often require specialized ATS equipment and knowledge of safe operational practices to avoid damaging the equipment further. Engaging professionals ensures that repairs not only restore functionality but also enhance the reliability and safety of the generator motor system.
- When experiencing persistent vibrations that may signal mechanical failure.
- If you suspect electrical faults or safety hazards in the system.
- When facing high-voltage components that require expert handling.
- If the generator motor fails to activate or provide temporary power.
- Upon noticing visible wear or damage to essential components.
- When complicated repairs exceed your technical expertise.
- If routine maintenance highlights abnormalities needing professional assessment.
DIY Maintenance Tips for Generator Motors
Regular maintenance of generator motors is crucial for prolonging equipment life and ensuring reliable stand-by power systems. Performing scheduled maintenance reduces long-term costs associated with unexpected repairs. One effective practice includes bearing inspections, as these components are vital for smooth motor operation. Consistent checking of bearings and other critical parts can catch problems early, preventing more extensive generator motor repair down the line.
Utilizing the right test equipment is essential for diagnosing issues efficiently. Regularly monitoring the performance of the generator motor helps maintain optimal power output. Simple checks such as oil levels, filter cleanliness, and electrical connections can greatly enhance the longevity of the system. Keeping a log of these maintenance activities can also help track performance and highlight any recurring issues that may need professional attention.
Conclusion
Understanding the intricacies of generator motor repair is crucial for maintaining the efficiency and longevity of these vital components. Regular assessments and timely repairs can prevent minor issues from escalating into significant failures. Familiarity with common problems and maintenance techniques empowers users to make informed decisions regarding repairs. By recognizing the signs that indicate the need for generator motor repair, operators can ensure that their equipment remains in optimal condition. This proactive approach not only enhances performance but also extends the lifespan of the generator motor, ultimately leading to cost savings and increased reliability.
FAQS
What should I do if my generator motor is not starting?
If your generator motor is not starting, check the fuel levels, battery charge, and connections. Ensure there are no blown fuses or tripped circuit breakers. If the problem persists, it may require professional diagnosis.
How often should I perform maintenance on my generator motor?
Regular maintenance should typically be performed every 50 to 100 hours of operation or at least once a year, depending on usage. This includes oil changes, filter replacements, and general inspections.
What are some common issues with generator motors?
Common issues include starting problems, overheating, unusual noises, vibrations, and poor performance. A bad motor PTC can sometimes be the problem as well. Regular maintenance can help prevent many of these issues.
Can I repair my generator motor myself?
Yes, many minor repairs and maintenance tasks can be done as DIY projects if you have the necessary skills and tools. However, for complex issues or safety concerns, it is advisable to seek professional help.
What tools are essential for generator motor repair?
Essential tools include a multimeter, wrenches, screwdrivers, pliers, a torque wrench, and safety equipment such as gloves and goggles. Depending on the repair needed, additional specialized tools may also be required.
How can I diagnose electrical problems in my generator motor?
To diagnose electrical problems, use a multimeter to check voltage and continuity in circuits. Inspect wiring for damage, and test components like relays and capacitors for functionality.
What is motor rewinding, and when is it necessary?
Motor rewinding involves replacing the wire coils in an electric motor's stator or rotor. It becomes necessary when the existing coils are damaged or burnt out, leading to poor performance or failure.
What are some DIY maintenance tips for generator motors?
DIY maintenance tips include regularly checking and changing the oil, cleaning or replacing air filters, inspecting spark plugs, and ensuring all electrical connections are secure and free of corrosion.
When should I seek professional help for generator motor repair?
Seek professional help when you encounter complex problems you are not comfortable troubleshooting, if there are safety concerns, or if your attempts at DIY repairs do not resolve the issues.
How can I prevent overheating issues in my electric motor?
To prevent overheating, ensure proper ventilation, regularly clean dust and debris from the motor, check for proper lubrication, and monitor load conditions to avoid overloading the motor.
What are some common electrical services involved in industrial/commercial generator maintenance for electric motors and generators power systems?
Common electrical services involved in industrial/commercial generator maintenance include ac motor inspections, scheduled maintenance costs assessments, and generator repair ips evaluations. Additionally, services often cover four wheel drive applications, industrial motor checks, fuel management services, and wicket gate repair to ensure that the motor runs efficiently and reliably.
How is commercial generator repair affected by the design of electric motor built components within generators power systems?
Commercial generator repair can be significantly impacted by the quality and design of the electric motor built components. Proper functioning of these components is crucial for the overall performance, efficiency, and longevity of generators power systems. If the electric motor built is not designed to handle the load or is not properly maintained, it can lead to frequent repairs and operational downtime in commercial generator applications.
What are the steps involved in the process of generator motor repair?
The process of generator motor repair typically involves several key steps including diagnosis of the issue, disassembly of the generator, inspection of all components, replacement of damaged parts, reassembly, and testing to ensure the generator operates correctly after the repair. Proper maintenance and timely repairs can extend the lifespan of a generator and ensure it functions efficiently.
What preventive measures can be taken to ensure the longevity of generator motors during routine maintenance?
Preventive measures for ensuring the longevity of generator motors include performing regular inspections, replacing worn parts promptly, keeping the motor clean, monitoring operating temperatures, and ensuring proper lubrication. Regular maintenance helps to prevent unexpected breakdowns and extends the lifespan of the generator motor.
What factors should be considered for effective generator motor repair in industrial settings?
Effective generator motor repair in industrial settings should consider aspects such as the design of components, preventive maintenance strategies, and the integration of electrical services to ensure optimal performance and longevity.