Comprehensive Guide to Electric Motor Repair and Maintenance for Efficient Motor Performance
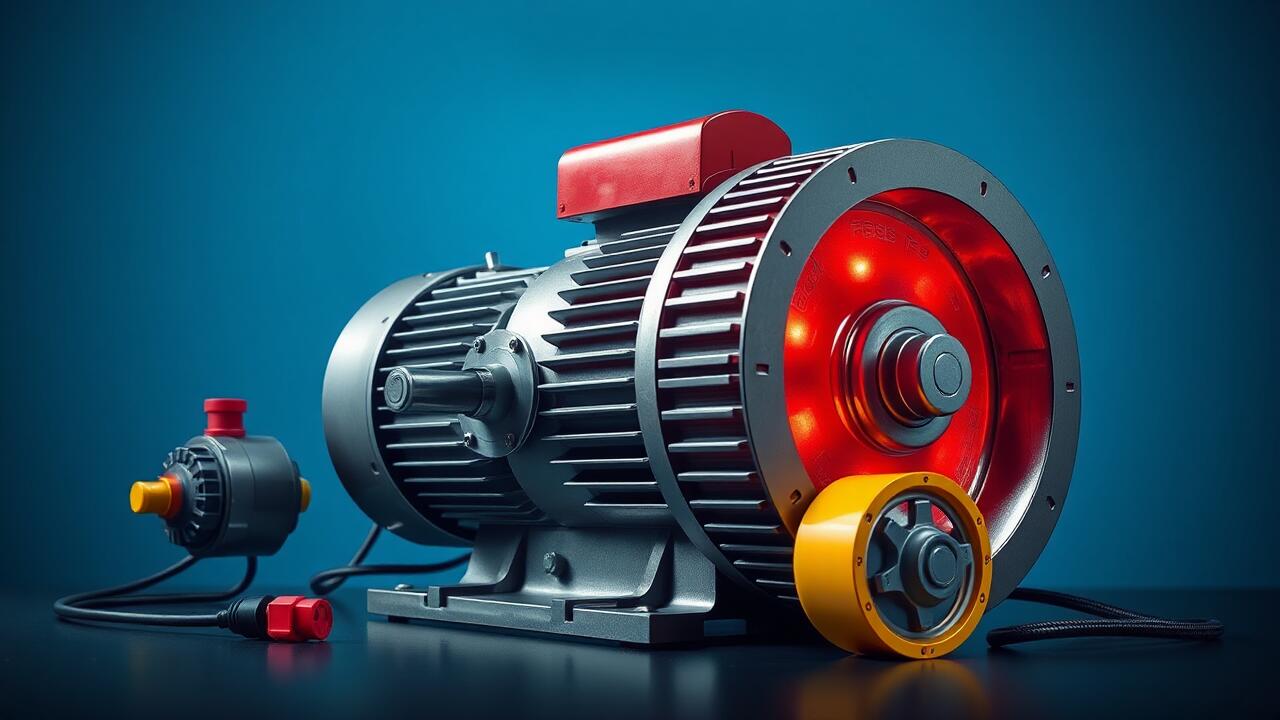
Table Of Contents
Key Takeaways
- Comprehending Electric Machinery
- Summary of Electric Machinery Restoration
- Electric Machinery Troubleshooting
- Electric Machinery Rewinding Process
- Electric Machinery Coating
- Lewis Machinery Restoration Methods
Understanding Electric Motors
Electric motors are essential devices that convert electrical energy into mechanical energy, powering a wide array of applications in industries and everyday life. These machines can be categorized into various types, including DC motors and AC motors, each serving distinct functions. Understanding the components of electric motors is crucial for effective electric motor repair, as issues can arise from wear and tear or electrical faults. Proactive maintenance and timely repairs ensure optimal performance and longevity of electrical motors, reducing downtime and costs associated with motor failures. Mastering the intricacies of these machines will lead to more informed decisions regarding repair and maintenance practices for both DC motors and other types of electric motors.
Components of Electric Motors
Electric motors consist of several key components that work together to convert electrical power into mechanical energy. The main parts include the stator, which is the stationary part that generates a magnetic field, and the rotor, which is the rotating component connected to the output shaft. Understanding these components is essential for effective electric motor repair, especially in motors like General Electric and universal motors that are widely used in various applications. Properly functioning components ensure that the motor operates efficiently at its specified voltage and current ratings.
Another crucial aspect of electric motors is their windings, which are coils of wire that create magnetic fields when electrical power is applied. These windings can be a common source of issues during electric motor repair, as they may experience wear or damage over time. Ensuring the integrity of the windings and other components can significantly improve motor performance and longevity. With regular maintenance and timely attention to repairs, issues in components can be addressed before they lead to more significant failures in electric motors.
Types of Electric Motors
Electric motors can be categorized based on their operational principles and design features. Common types include induction motors and synchronous motors, each with unique characteristics suited for different applications. Induction motors, widely used in industries, rely on rotating magnetic fields generated by coils. Brands like Baldor Electric and Emerson Electric offer reliable models that contribute to machine efficiency. Understanding these distinctions helps in determining the right electric motor repair strategies when issues arise.
Another classification focuses on the supply of electrical energy. AC (alternating current) motors are versatile choices for various machines, while DC (direct current) motors provide precise speed control. Each type has specific coil configurations that influence performance and energy consumption. This knowledge aids technicians in effective troubleshooting and electric motor repair, ensuring optimal operation and longevity of the equipment.
Overview of Electric Motor Repair
Electric motor repair involves a comprehensive understanding of the various components that contribute to machine functionality. Problems with the rotor can significantly affect performance, necessitating precise diagnostics and skilled intervention. Bearings and gearboxes often wear down over time, leading to inefficiencies or outright failure. Techniques such as welding may be employed to restore damaged parts, while the overall repair process requires a systematic approach to ensure longevity. By addressing these issues promptly, electric motor repair extends the life of equipment and maintains operational efficacy.
Common Issues in Electric Motors
Electric motors, both AC and DC types, can experience a variety of issues that necessitate electric motor repair. Common problems include insulation breakdown, which can lead to electrical shorts, and winding failures that impact performance. Vibration analysis is a useful diagnostic tool for identifying mechanical issues, such as misalignment or bearing wear, which can affect the overall efficiency of the motor. In pumps, this can result in reduced performance and increased energy consumption.
Overheating is another prevalent concern, often resulting from excessive load or insufficient cooling. This can cause premature failure of the windings and insulation materials, leading to the need for significant repairs. Regular maintenance and timely electric motor repair can mitigate these issues. Proactive assessments and repairs can extend the life of electric motors and ensure their optimal function in various applications.
Benefits of Timely Motor Repair
Timely industrial electric motor repair is crucial for maintaining optimal performance and extending the lifespan of motors. Addressing issues as they arise can prevent minor problems from escalating into significant failures. A proactive approach to motor repair not only reduces downtime but also minimizes the costs associated with large motor repair. Engaging with a reputable manufacturer for electric motor refurbishment ensures that repairs are conducted with high-quality standards.
Regular maintenance and prompt electric motor repair can enhance overall efficiency, leading to energy savings and improved productivity. Unattended issues can result in more severe damage, requiring extensive electric motor repair efforts that could have been avoided. By investing in timely maintenance, businesses can optimize their motor systems and avoid the disruptions associated with unexpected breakdowns.
Electric Motor Diagnostics
Effective diagnostics play a critical role in electric motor repair, enabling technicians to identify issues before they escalate. An electric motor company relies on advanced tools to assess the condition of components, including the electric motor shaft, which is pivotal for optimal performance. By understanding how an electric motor combines various mechanisms, technicians can pinpoint failures that may require electric motor rewinding. Specialized techniques such as lewis motor repair also benefit from detailed diagnostic processes, ensuring that repairs are both efficient and lasting. Accurate interpretation of diagnostic results informs the best course of action, enhancing the longevity and reliability of electric motors.
- Regular maintenance and inspections can prevent unexpected failures.
- Utilizing vibration analysis can help identify misalignments and wear.
- Resistance testing is essential for assessing insulation health.
- Thermal imaging can detect overheating components before damage occurs.
- Periodic lubrication checks can prolong motor life and efficiency.
- Comprehensive documentation of diagnostics aids in trend analysis over time.
- Investing in advanced diagnostic tools can improve repair accuracy and speed.
Tools for Effective Diagnostics
Effective diagnostics for electric motor repair require a variety of specialized tools. Multimeters are essential for measuring voltage, current, and resistance in AC/DC motors. Analyzing these parameters helps identify electrical failures that could lead to the need for an electric motor rewind. Oscilloscopes can also be utilized to visualize electrical waveforms, providing deeper insights into the performance of electric motors and aiding in mechanical repairs.
Thermal imaging cameras have become popular for diagnosing issues without direct contact. These tools detect hot spots in motors, indicating potential problems in areas such as winding or bearings. For pool motor repair, a combination of these diagnostic tools streamlines the troubleshooting process, ensuring accurate identification of faults. Proper diagnostics ultimately lead to more efficient electric motor repair, enhancing the longevity and reliability of the equipment.
Interpreting Diagnostic Results
Understanding diagnostic results is crucial for effective electric motor repair. Experienced motor technicians analyze various parameters to determine motor health. This evaluation often involves checking the efficiency of motor insulation methods. Identifying issues early can prevent more extensive damage and costly pump repair.
Proper interpretation of diagnostic findings guides the decision-making process for repairs or replacements. Sometimes, repairs might lead to the recommendation of new motor sales if the existing unit is beyond economical repair. Ensuring clarity in these results can significantly influence the longevity and performance of the electric motor.
Electric Motor Rewinding
Rewinding is a crucial process in electric motor repair, addressing the deterioration commonly observed in coil motors. This procedure becomes essential for maintaining the efficiency of various types of motors, including 3-phase motors, which are widely used in industrial applications. Recognizing the signs that indicate the need for rewinding can significantly prolong the lifespan of electric motors, ultimately reducing the frequency of gearbox repair and other specialized repairs. Understanding the rewinding process not only enhances motor performance but also plays a vital role in comprehensive electric motor repair strategies.
- Regularly inspect motors for signs of wear and tear, such as unusual noises or overheating.
- Monitor electrical resistance and current draw to identify potential issues early on.
- Keep a record of motor performance to track any changes over time.
- Use high-quality insulation materials during the rewinding process to enhance durability.
- Ensure proper alignment and balance of the rotor after rewinding to prevent future failures.
- Train staff on best practices for motor maintenance to minimize the risk of damage.
- Consult professionals for complex rewinding tasks or when specialized equipment is needed.
Signs That Rewinding is Necessary
A noticeable drop in the performance of an electric motor often indicates the need for rewinding. Symptoms such as overheating, unusual noises, or increased vibration can be warning signs. These issues typically stem from damaged coils or shorts within the windings, necessitating specialized electric motor repair. Electrical testing is essential in diagnosing the precise nature of the problem, guiding the repair services toward an effective solution.
Another clear indicator that rewinding is necessary involves physical signs like burnt or discolored insulation. This deterioration can lead to significant failures if left unaddressed, making timely repairs crucial. Using techniques like automated coil winding can enhance the efficiency of the repair process, ensuring that the motor is restored to optimal functioning. Properly executed electric motor repair not only resolves existing issues but also prolongs the lifespan of the equipment.
The Rewinding Process Explained
Rewinding an electric motor involves several critical steps to ensure proper function and longevity. Initially, the technician must disassemble the motor to access the stator and rotor components. Once the parts are exposed, any damaged coils or wire are identified. Replacing open coils or wire is essential to restore electrical tolerances, which significantly affect the motor's performance. The quality of the new coils directly impacts the motor's efficiency and capacity to withstand equipment deterioration over time.
After replacing the damaged sections, technicians proceed to rewind the coils with the appropriate gauge wire. This process requires precision since incorrect winding can lead to imbalances in machine shafts and contribute to further mechanical issues. Once rewinding is complete, the motor is reassembled and thoroughly tested. Proper electric motor repair not only rectifies existing problems but also enhances the durability of the motor, making it crucial for maintaining operational efficiency.
Electric Motor Varnishing
Varnishing plays a crucial role in electric motor repair, serving as a protective layer that enhances the longevity and performance of new coils. A skilled mechanic must conduct precise mechanical measurements to ensure the correct application of varnish, which directly impacts the reliability of the motor. Techniques such as motorsafe stripping are often employed before varnishing to remove any contaminants and prepare the surface. For Russell Motors, this process is vital to maintain optimal operational efficiency and reduce the risk of failures. Proper varnishing not only safeguards the internal components but also simplifies future electric motor repair endeavors, leading to more effective maintenance practices.
Importance of Varnishing in Motor Maintenance
Varnishing plays a crucial role in the maintenance of electric motors, particularly for random-wound motors. The varnish acts as a protective layer for the coils, preventing moisture and dust from compromising their integrity. This protection helps extend the life of the motor and minimizes the need for electric motor repair. Ensuring that the varnish maintains its quality is essential for optimal performance and efficiency, especially in applications that involve high torque and full nameplate voltage.
Regular varnishing also supports proper operation during soft start repair situations. A well-maintained varnish layer can enhance the resilience of the motor against wear and tear, which is vital for operations involving gearbox sales. By prioritizing varnishing in an electric motor maintenance routine, operators can effectively reduce downtime and expensive repairs.
Methods of Electric Motor Varnishing
Varnishing is a critical step in electric motor repair, especially for fractional motors that operate under demanding conditions. This process involves applying a protective layer to the windings, ensuring that the insulation remains intact as the rotor spins. Proper varnishing techniques strengthen the form coil and prevent moisture ingress, which can lead to equipment failures. A well-varnished motor can significantly enhance its longevity and performance under varying loads.
Several methods are available for varnishing electric motors, each tailored to specific applications and equipment. The dip and bake method is commonly used, where the motor is immersed in varnish and then heated to facilitate curing. Spray varnishing is another effective technique, allowing for even coverage on intricate parts. Some services even offer welding service alongside varnishing to address any physical damage during the repair process. Selecting the right method is essential for ensuring optimal protection and performance of the motor.
Lewis Motor Repair Techniques
Repairing Lewis motors requires specialized approaches tailored to the unique needs of these systems. Common electric motor repair tasks often involve the replacement of worn bearings, which are crucial for smooth operation. In many cases, issues arise with the pumps linked to the motor, necessitating a thorough assessment of the gearbox needs to ensure optimal performance. If a motor's efficiency declines, a new shaft may be required to restore function, improving overall reliability. Understanding these aspects is essential for effective electric motor repair and ensuring the longevity of the equipment.
Specialized Approaches for Lewis Motors
Electric motor repair for Lewis Motors requires a tailored approach to address their unique designs, particularly those found in Fasco motors and Packard models. Technicians must be proficient in using modern equipment, ensuring they have the right tools to diagnose issues accurately. Attention to detail is crucial, especially when measuring components like the output shaft diameter, which can significantly impact motor performance during maintenance.
The specialized repair techniques for Lewis Motors often include a thorough analysis of the motor's construction and operational history. Technicians adapt their methods based on the specific needs of each model, seeking to enhance longevity and efficiency. By integrating advanced technologies and adhering to best practices, effective electric motor repair can preserve the integrity of these essential machines, ensuring they operate optimally over time.
Case Studies in Lewis Motor Repair
Case studies in Lewis Motor Repair reveal the intricacies involved in restoring electric motors to optimal functionality. One notable case highlighted an electric motor suffering from damaged shafts and worn-out blades. The repair process included meticulous inspection, followed by precise winding techniques to ensure the motor's efficiency was restored. Engineers focused on the alignment of the wheels to eliminate vibrations that can lead to further wear and tear.
Another case addressed a Lewis motor with severe overheating issues. The diagnostic process uncovered a short circuit due to worn insulation on the winding, requiring detailed electric motor repair. Following rewinding with high-quality materials, technicians applied varnishing to enhance insulation and prolong lifespan. Such case studies emphasize the importance of targeted interventions and the comprehensive understanding of motor components for effective repair solutions.
Conclusion
An effective approach to electric motor repair requires a comprehensive understanding of the various components and their functions. Identifying common issues early can save time and resources, while timely interventions can extend the lifespan of the motor. Repairing or replacing faulty parts is crucial to maintaining optimal performance. Emphasizing routine diagnostics and maintenance can prevent more significant problems down the line. Through proper care and attention, electric motor repair can ensure that motors operate efficiently, minimizing downtime and enhancing productivity in various applications.
FAQS
What are the common signs that my electric motor needs repair?
Common signs include unusual noises, overheating, reduced performance, vibrations, and frequent tripping of circuit breakers.
How often should I have my electric motor serviced?
It is generally recommended to have your electric motor serviced annually, but the frequency may vary based on usage, environment, and manufacturer guidelines.
What is the difference between electric motor rewinding and repair?
Rewinding involves replacing the motor's coils to restore its functionality, whereas repair can include fixing or replacing any failing components without rewinding.
Can I repair an electric motor myself, or should I hire a professional?
While some minor repairs can be done by knowledgeable individuals, it is often best to hire a professional for safety and to ensure the repair is done correctly.
What tools are essential for electric motor diagnostics?
Essential tools include multimeters, insulation resistance testers, vibration analyzers, and thermal imaging cameras for effective diagnostics.
What are the common issues encountered in electric motors repair, especially concerning coils/wire and new shafts?
During electric motors repair, common issues often involve damage to coils/wire and the need to replace open coils/wire. Additionally, when repairing electric motors, it may also be necessary to install new shafts to ensure optimal performance.
What steps should be taken for effective electric motor repair, particularly in diagnosing coil issues and replacing worn shafts?
For effective electric motor repair, it is essential to conduct a thorough diagnosis of coil issues and assess whether the shafts are worn out. Start by checking the electrical connections and testing the coils for continuity. If coil issues are detected, they may need to be re-wound or replaced. For worn shafts, measure them for wear and check for any misalignment. Proper maintenance and regular inspections can help prevent these problems in the future.
What tools and equipment are essential for successful electric motor repair, particularly when dealing with coil restoration and shaft alignment?
To ensure successful electric motor repair, it's crucial to have specific tools and equipment. For coil restoration, you will need tools like a multimeter for testing electrical continuity, soldering equipment for repairing or replacing wire connections, and specialized coil winding tools if rewinding is necessary. When it comes to shaft alignment, precision tools like dial indicators or laser alignment systems are important to achieve proper alignment and reduce wear on bearings. Having the right tools not only aids in diagnosing issues but also enhances the overall quality of the repairs.
How can one ensure the longevity of an electric motor after repair, particularly in relation to coils and shafts?
To ensure the longevity of an electric motor after repair, it’s important to conduct regular maintenance checks focusing on the coils for any signs of wear or damage, and making sure that shafts are properly aligned and lubricated. This includes monitoring the conditions under which the motor operates and addressing any issues with wiring or shaft integrity promptly to avoid future repairs.
What preventative maintenance practices are recommended for electric motor repair, especially for maintaining coils and shafts?
Preventative maintenance for electric motor repair should include regular inspections of coils and shafts to identify any wear or damage before they lead to major failures. It is also important to keep the motor clean and lubricated, check for proper alignment of the shafts, and ensure that connections are secure. Regular monitoring of electrical parameters can help in detecting issues with coils early, thus improving the overall reliability and efficiency of the motor.