Comprehensive Guide to DC Electric Motor Repair and Maintenance Techniques
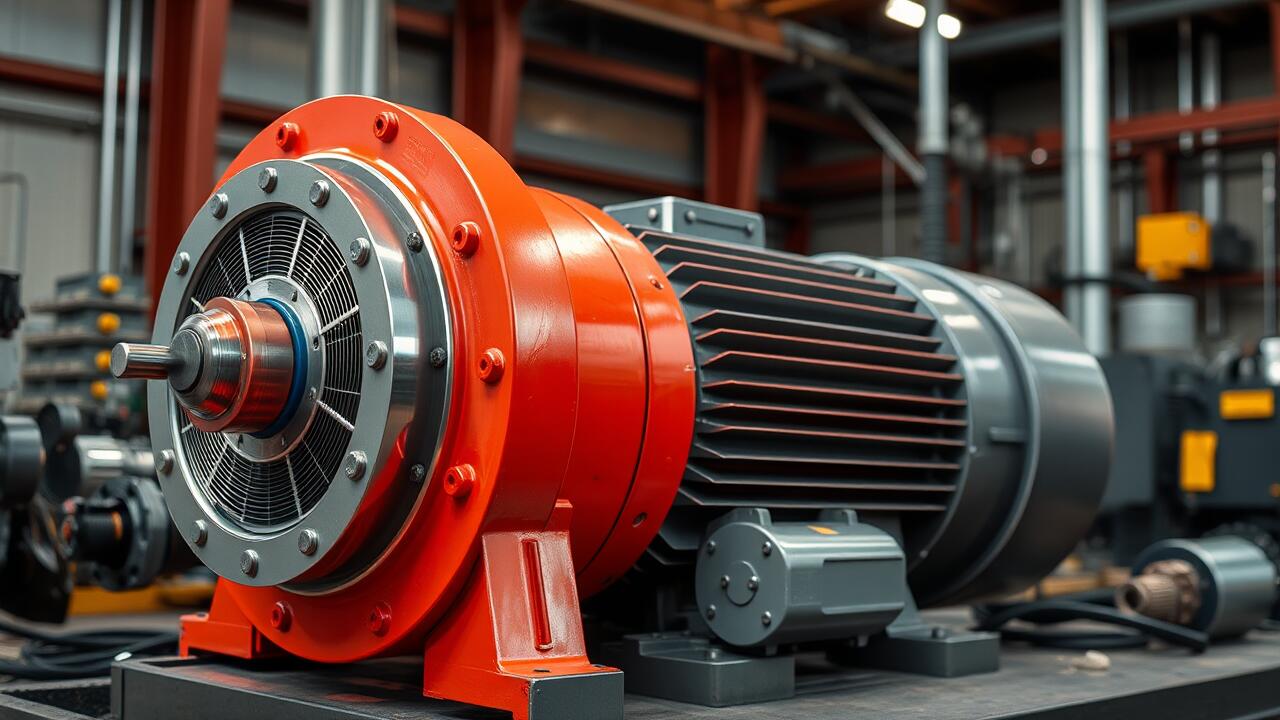
Table Of Contents
Key Takeaways
- Comprehending direct current electric engines and their functionality
- Frequent problems associated with direct current electric engines
- Significance of repairing direct current electric engines
- Procedures involved in repairing direct current engines
- Techniques for repairing electric engines
- Rebuilding electric engines compared to repairing them
- Specialized services for engine repairs
- Maintenance advice for direct current electric engines
Understanding DC Electric Motors
A DC electric motor is a vital component widely used in various applications, ranging from small household appliances to large industrial machines. Understanding its operational principles and components is crucial for effective maintenance and troubleshooting. Regular dc electric motor repair ensures optimal performance and longevity of these electric motors. Over time, wear and tear on dc motors can lead to malfunctions, making timely repairs essential. Familiarity with common components and the functioning of a DC motor enables users to recognize potential issues early, thus minimizing downtime. Proper care and maintenance, including periodic inspections, play a significant role in the efficient operation of these electrical motors.
Components of a DC Electric Motor
A DC electric motor consists of several key components, each crucial to its motor function. The armature, or rotor, is responsible for the rotation and is typically made of wire windings. Stators provide the magnetic field necessary for the motor to operate. Brushes and a commutator are essential in maintaining a steady electric current flow, converting direct current into mechanical energy. These components work synergistically, allowing the motor to control speed and torque efficiently. Understanding these elements is vital for effective dc electric motor repair in the motor industry.
Another important aspect of a DC electric motor is its electrical and mechanical interactions. The starter motor is vital for initiating movement, requiring the right voltage to function efficiently. AC motors operate on alternating current principles, contrasting with DC motors that utilize direct current. This distinction is significant for repair technicians who specialize in both types of motors. Knowledge of these components greatly enhances the effectiveness of dc electric motor repair and troubleshooting in various applications.
How DC Motors Function
DC motors operate through the interaction of magnetic fields and electric currents. Inside these motors, electricity flows through the coils, generating a magnetic field that interacts with permanent magnets or other coils. This process results in rotational motion, enabling the motor to power various mechanical systems. Regular maintenance and repairs are essential to ensure optimal performance, particularly in settings where motors are used alongside AC/DC converters and electronic equipment. Understanding the function of your motor can help anticipate potential issues and reduce the need for extensive dc electric motor repair.
The efficiency of DC motors can sometimes be affected by factors such as voltage fluctuations or wear and tear over time. High voltage situations or improper maintenance can lead to increased wear on components, necessitating timely repairs. Unlike induction motors and transformers, which primarily rely on alternating current, DC motors are particularly sensitive to electrical disturbances. Establishing a routine inspection schedule helps identify problems early, ensuring that both regular maintenance and repairs are carried out efficiently for longevity and reliability in various applications.
Common Issues with DC Electric Motors
DC electric motors are prone to various issues that can hinder their performance and longevity. Common problems may arise from faulty wiring, leading to inefficient operation or complete failure. Brush shifting motors often experience issues with their brushes, which can result in excessive wear on the coils. A malfunctioning servo motor might fail to respond adequately to control signals, affecting overall functionality. Battery-related issues can also cause a lack of power to the motor, impairing its ability to start or operate at optimal levels. Inspecting components such as the drive shaft for misalignment or wear is vital, as these factors can contribute to further damage. Timely dc electric motor repair is crucial to address these problems and prevent more significant failures down the line.
Diagnostic Signs of Motor Failure
A variety of symptoms can indicate a failing DC electric motor. Users should be aware of excessive electrical noise during operation, which may signal internal issues. An ac generator might also exhibit similar behavior, hinting at problems that could necessitate dc electric motor repair. Observing unusual vibrations or overheating can further indicate mechanical wear or electrical overload. In such instances, using a screwdriver to inspect connections and components may uncover potential faults that require immediate attention.
Unexpected performance changes can also serve as warning signs. A motor that struggles to start or operates intermittently may indicate worn coils or faulty electrical connections. These issues can lead to inconsistent power distribution and decreased efficiency. Regular monitoring and timely dc electric motor repair can help avoid more significant problems in the future, ensuring the longevity of the electromechanical systems in which these motors are used. Addressing these signs early will often save time and resources in the long run.
Causes of DC Electric Motor Malfunctions
Several factors can lead to malfunctions in DC electric motors, impacting their efficiency and performance. Common issues include wear and tear on components, such as bearings and commutators. These problems can arise in various applications, including servo motors, pumps, and hydraulic equipment. The use of substandard magnet wire in the winding process can also result in overheating, leading to premature failure. Regular maintenance is essential to identify these issues early and seek timely DC electric motor repair.
Electrical failures often occur due to insulation breakdown or short circuits, particularly in permanent magnet motors. Dust, debris, and moisture accumulation can hinder the motor's operation, causing significant problems if not addressed. Improper connections and voltage fluctuations can further exacerbate malfunctions. Identifying the root causes promptly allows for effective dc electric motor repair, ultimately extending the lifespan of machines and improving overall reliability.
The Importance of DC Electric Motor Repair
Understanding the significance of timely dc electric motor repair can greatly enhance the longevity and performance of various machines. Regular maintenance not only prevents unexpected failures but also ensures that components like the rotor and printed circuit board function optimally. In applications such as compressors and robotics, where precision and torque are critical, neglecting repairs can lead to decreased efficiency and increased operational costs. Addressing issues promptly can not only extend the lifespan of the motor but also improve overall system reliability, making frequent inspection and proactive repair strategies essential.
Benefits of Timely Repairs
Timely dc electric motor repair ensures that pumps and other machinery operate efficiently and effectively. Addressing issues as soon as they arise prevents minor problems from escalating into major failures. Regular maintenance and prompt dc motor repair can extend the life of the equipment, ultimately leading to reduced downtime and better productivity in operations that rely on electric motors.
Neglecting to perform timely repairs on dc electric motors can result in increased costs and complex motor repair work. Failure to repair issues promptly may lead to more extensive damage, necessitating a complete replacement rather than simple electric motor repair. Investing in repairing dc motors not only enhances performance but also fosters a more reliable and cost-efficient operation.
Cost-Effectiveness of Repairing over Replacing
The choice between repairing and replacing a DC electric motor can significantly impact budget considerations. Investing in DC electric motor repair often provides immediate cost savings compared to the expenses associated with new electric motor installation. With expert motor repair services available, routine repairs can extend the lifespan of existing equipment. This not only aligns with the financial interests of businesses but also supports sustainability within the electric motor industry by reducing waste.
Electric motor diagnostics play a crucial role in identifying issues that can be resolved through effective repairs such as electric motor rewinding. This process can restore motors to optimal performance without the hefty price tag of purchasing a new unit. Understanding the value of skilled electric motor services can lead to better decision-making. Cost-effective repairs ensure that businesses maintain their operations efficiently without incurring unnecessary expenditures.
Steps for DC Motor Repair
Effective DC electric motor repair involves a systematic approach to ensure optimal performance post-repair. The initial assessment is critical, allowing technicians to diagnose issues related to motor failures that may arise from wear and tear or improper motor installation. Following this, a thorough disassembly and inspection process helps identify specific mechanical repairs needed. Common repairs often include rewinding coils or addressing component failures, especially in servo motor repairs. Utilizing a qualified current motor shop ensures that the necessary expertise is applied throughout the repair process, ultimately restoring the functionality of the powered motor. Regular maintenance after repairs enhances longevity, making attention to these steps crucial in avoiding future complications.
Initial Assessment and Troubleshooting
A thorough initial assessment of a DC electric motor is crucial for effective repair. Evaluating the condition of motor components allows technicians to identify potential issues impacting motor efficiency. Observing the drive motor's performance can reveal anomalies that may indicate the need for immediate attention. Recognizing these signs early prevents further damage that could lead to costly industrial motor replacements or complicated pump repair processes.
Troubleshooting involves systematic checks of various motor functions and examining rebuilt motors to ensure they meet operational standards. Technicians should test voltage levels and inspect wiring connections to pinpoint faults. Proper diagnostics during this phase can streamline the DC electric motor repair process, ultimately enhancing the longevity and reliability of the motor in its application.
Disassembly and Inspection Process
Disassembling a DC electric motor requires careful attention to detail. Remove any external components and secure all screws and fasteners in a designated area to avoid confusion. Inspect old motor windings for signs of wear or damage, as this is a common issue in many motor failures. Proper handling during disassembly ensures that components remain intact, making the subsequent inspection process smoother.
Once the motor is disassembled, a thorough inspection should be conducted on all parts, including the motor bearings. Motor bearing failure is a frequent cause of operational issues in electric motors. Assessing the condition of old motor components allows for timely identification of necessary replacements and helps establish a maintenance and dc electric motor repair plan that includes appropriate repair frequency.
Common Repairs and Replacements
DC electric motor repair often involves addressing common issues related to electrical loads and component wear. Repair capabilities include examining motor prints to pinpoint areas of concern, such as deteriorating windings or faulty electrical connections. Motor rewind departments play a critical role in restoring functionality, ensuring that the coils within the motor are rewound to meet original specifications. A pristine motor is essential for optimal performance, making timely repairs vital.
Replacing damaged parts is another key aspect of ensuring a motor's longevity. Common repairs may involve inspecting the motor casing for cracks or signs of wear, which can affect performance. Components such as bearings may require replacement as they are crucial for smooth operation, allowing the motor to resist excess friction. Addressing these issues promptly can help maintain the efficiency of a DC electric motor and extend its operational lifetime.
Electric Motor Repair Techniques
DC motor repair involves a variety of techniques tailored to restore functionality and efficiency in various applications. For industrial motors, understanding the specific components such as motor caps and exposed motors is crucial for effective intervention. Repairing hydraulic equipment often requires similar principles, as both systems rely on precise functionality. An effective repair process starts with assessing how the motor passes electrical signals, crucial for diagnosing issues. Car starter motor repairs highlight unique challenges that may differ from standard industrial repairs but share the fundamental goal of operational reliability. Employing accurate techniques not only extends the lifespan of these motors but also enhances overall performance across diverse applications.
Rewinding Coils in DC Motors
Rewinding the coils of a DC electric motor is a crucial aspect of DC electric motor repair. Motors accumulate wear and tear over time, leading to damaged windings that can significantly affect performance. Precision electric repair services utilize specialized techniques to replace corroded or burnt windings, ensuring that the motor operates at optimal efficiency. Quality repair services are essential for maintaining the integrity of motors within power distribution equipment, as compromised windings can lead to further system failures.
The process involves removing the existing windings and carefully measuring the dimensions of the core. This allows for the creation of new windings that meet the original specifications. Technicians employ high-quality materials to reinforce durability and enhance performance. Properly executed, rewinding not only restores functionality but also extends the lifespan of the DC motor, showcasing the importance of expert DC electric motor repair in the overall maintenance strategy.
Bearing Replacement Procedures
Replacing bearings in a DC electric motor is a critical aspect of maintaining optimal performance. During the dc electric motor repair process, technicians often identify worn or damaged bearings that can lead to expensive repairs if not addressed promptly. Repair shops equipped with specialized tools like a coil-winding machine can facilitate these certain repairs, ensuring that the motor runs smoothly and efficiently after the replacement.
Experienced repair technicians follow a structured approach to bearing replacement. This involves disassembling the motor, removing the old bearings, and installing high-quality replacements. Proper alignment and lubrication are essential to prevent premature wear and ensure longevity. Comprehensive repair services often encompass this procedure, allowing for a thorough maintenance check that safeguards against potential future issues.
Testing Motor Performance Post-Repair
A thorough evaluation of motors performance is crucial after dc electric motor repair. This step helps identify if the repair was successful and whether any mechanical damage remains. New coils must be tested for proper connectivity and functionality. For spindle drive motors, ensuring the mechanical operation aligns with specifications is vital to prevent future failures.
Post-repair testing often involves running the motor under load conditions to assess its performance. The entire repair process should be validated to confirm that the motor operates efficiently. If issues arise during testing, further investigation may be necessary to address any underlying problems that could affect the motor's longevity.
Electric Motor Rebuild vs Repair
Rebuilding a DC electric motor can be a strategic choice under specific circumstances. Several reasons motors may require this extensive service include significant wear on internal wiring, excessive electrical stress, or persistent issues stemming from defective bearings. A rebuild often addresses these challenges comprehensively, restoring power outputs to optimal levels. In-house repair may suffice for minor problems, yet more severe conditions often necessitate a thorough overhaul to prevent further repairs down the line. Understanding the conditions that warrant a rebuild versus simple repair is essential for maintaining the longevity and performance of DC electric motors.
When to Rebuild an Electric Motor
Rebuilding an electric motor often becomes necessary when the wear and tear exceed the limits of what can be addressed through standard DC electric motor repair. Extra-large motors, in particular, may require a rebuild due to extensive damage that compromises their efficiency and reliability. Shops specializing in quality repairs may recommend a rebuild when components such as windings or rotor assemblies are significantly degraded. Proper rebuilding ensures that high-quality repairs are implemented, restoring the motor to optimal functioning conditions.
Consideration for rebuilding also hinges on the cost-effectiveness of the operation. Some motors may be too far gone for simple repairs, leading to prolonged downtime and inefficient operations. Many motor shops can provide long-lasting repairs using motor-specific paints and components, which extend the life of the motor. Choosing to invest in rebuilding rather than a complete replacement can result in substantial savings and a reliable, rejuvenated electric motor.
Steps Involved in an Electric Motor Rebuild
Rebuilding a DC electric motor involves several essential steps ensuring optimal performance and longevity. The process begins with disassembling the motor housing to access internal components. Careful handling of machine shafts and driven equipment is crucial during this phase. Once disassembled, technicians can assess the condition of the windings and any potential damage. This phase often leads to replacing worn-out components, including installing new cables for improved conductivity, which contributes to a long-lasting repair.
After performing the necessary repairs, the motor undergoes thorough testing to verify its functionality. This includes checking the resistance of the windings and ensuring all connections are secure. Ongoing maintenance practices are vital to keep the motor in peak condition after its rebuild. A well-executed DC electric motor repair not only improves efficiency but also extends the lifespan of the fractional motor, making it a worthwhile investment for any operation reliant on such machinery.
Specialized Repair Services
Understanding the nuances of dc electric motor repair is critical for maintaining efficiency and longevity in various applications. Common issues like bad coils or broken wires can significantly impact performance, necessitating specialized skills for effective resolution. Technicians often address problems related to drive gears and spindle motors, which may require detailed equipment vibration analysis to identify underlying mechanical loads. For hi-lo motors, precise diagnostics become essential to ensure optimal functioning. By employing expert techniques, these services can restore motors to peak performance, ultimately extending their lifespan and reducing downtime.
AC/DC Motor Repair Techniques
Effective DC electric motor repair involves a variety of techniques that are crucial for restoring functionality. Skilled winding technicians play a significant role in this process, especially when there are issues with the coils. They often inspect the circuit board for damages and check the cables that connect the motor to its power source. The rear bearing shaft may also require attention, particularly if vibrations indicate potential failures. Authorized warranty repair services can provide assurance that repairs meet manufacturer standards, ensuring the longevity of the equipment.
Machine work is vital in performing accurate DC electric motor repairs that require specialized equipment. Technicians should be adept at diagnosing circuit faults and knowing when to replace components, such as bearings or circuit boards. Proper tools and methods ensure that the entire system operates smoothly. Regular maintenance checks can prevent many issues, making timely DC electric motor repair a cost-effective practice for any operation relying on these essential machines.
- Regularly inspect and clean motor components to prevent buildup and wear.
- Ensure proper alignment of motor parts to minimize vibrations and increase efficiency.
- Implement temperature monitoring to detect overheating and potential failure early.
- Use insulation testing to evaluate the condition of the windings.
- Keep an inventory of frequently replaced parts to reduce downtime during repairs.
- Train staff on basic troubleshooting techniques to identify issues before they escalate.
- Schedule periodic professional inspections to maintain optimal motor performance.
Finding Qualified Electric Motor Repair Technicians
Expertise in DC electric motor repair is crucial for maintaining and restoring the functionality of various industrial equipment. Technicians with experience understand the intricacies of components like VFD-rated magnet wire and the importance of precise re-insulation methods. They can effectively reinsert form coil windings, ensuring the machine part operates as intended, particularly for applications such as fork truck motors.
Choosing a qualified technician can significantly impact the longevity and performance of your DC electric motor. Professionals skilled in DC electric motor repair can diagnose issues quickly, perform necessary repairs, and provide valuable maintenance tips. Their knowledge ensures that the right techniques are employed, resulting in reliable operation and reduced downtime for your equipment.
Maintenance Tips for DC Electric Motors
Regular inspection practices are essential for prolonging the lifespan of DC electric motors. Engineers recommend checking internal components, such as capacitors and induction magnets, using a small screwdriver for accessible areas. Ensuring all equipment is secure and free of debris can minimize potential malfunctions. Scheduling routine maintenance not only aids in identifying early signs of wear but also supports timely dc electric motor repair. Investing in electronic services can enhance the performance of machines, making them more efficient and reliable. Implementing these proactive measures facilitates engineer improvements and reduces the likelihood of severe breakdowns in the long run.
- Regularly clean the motor and its surrounding area to prevent dust accumulation.
- Check and tighten all electrical connections to ensure optimal performance.
- Lubricate moving parts as recommended to reduce friction and wear.
- Monitor motor temperature to identify overheating issues early.
- Keep an eye on noise levels, as unusual sounds can indicate problems.
- Test the insulation resistance periodically to prevent electrical failures.
- Document and track maintenance activities for effective long-term management.
Regular Inspection Practices
Routine maintenance of DC electric motors is crucial for longevity and optimal performance. Regular inspections help identify potential issues early on, preventing costly dc electric motor repair down the line. All machine components, including the front bearing shaft, should be checked for wear and tear. Using dynamic balancing equipment and machines can aid in assessing the balance of rotating parts, ensuring efficient operation across different machines.
Implementing a systematic inspection protocol allows for timely identification of worn or damaged replacement parts. This proactive approach minimizes downtime and enhances productivity. Technicians should focus on the functionality of various machine components and utilize dynamic balancing machines to detect any imbalances that can lead to motor failure. Paying attention to these aspects will ultimately contribute to a more reliable and efficient operation of DC electric motors.
Conclusion
Understanding the intricacies of DC electric motor repair is crucial for maintaining optimal performance and longevity. Common signs of wear, such as vibration or unusual noise, often indicate issues like worn bearings that can affect a motor’s efficiency. Utilizing components like VFD-shielded wire enhances the durability of the motor during operation. For motors showing significant wear, generator rewinding and thorough inspections of the shaft and drive system are essential steps in the repair process. Regular maintenance allows early detection of issues, ensuring that timely dc electric motor repair can prevent more extensive damage and costly replacements.
FAQS
What is a DC electric motor?
A DC electric motor is a device that converts direct current electrical energy into mechanical energy, commonly used in various applications due to its simplicity and efficiency.
What are the common issues faced by DC electric motors?
Common issues include overheating, excessive noise, vibration, insufficient torque, and failure to start or run, often resulting from wear and tear, electrical faults, or mechanical failures.
How can I diagnose if my DC motor is failing?
Diagnostic signs of motor failure may include unusual noises, vibrations, overheating, changes in performance, or complete failure to operate. Checking for loose connections and testing voltage can also help.
Is it better to repair or replace a DC electric motor?
Repairing a DC electric motor is often more cost-effective than replacing it, especially if the damage is minimal and can be addressed through maintenance or repairs.
When should I consider rebuilding my DC electric motor?
Rebuilding may be necessary when the motor shows significant wear, persistent issues despite repairs, or when multiple components need replacement, making it more economical to rebuild than to repair.
What are some common issues that can arise during dc electric motor repair, specifically related to polyphase motors and worn bearings?
During dc electric motor repair, common issues can include problems with polyphase motors which may not function properly if the internal capacitors are failing. Additionally, worn bearings can cause increased resistance in the motor housing, hindering performance. It's essential to check the motor windings for damage and ensure that repairs will provide a long lasting repair, especially when dealing with hydraulic equipment repair. Motors should be maintained regularly to prevent these issues.
What causes issues with electric motor repair when it comes to motor winding failures and the impact of worn bearings?
In electric motor repair, problems can arise when motor windings fail due to overheating or insulation breakdown. Additionally, worn bearings can cause misalignment, leading to increased friction and heat, which might exacerbate the issues in the motor housing. Thus, it’s essential to inspect both motor windings and bearings during any repair process to ensure the longevity and efficiency of the electric motor.
How can worn bearings cause problems during the electric motor repair process?
During the electric motor repair process, worn bearings can cause increased friction, which leads to overheating and ultimately may damage the motor housing. When the bearings are worn, it can also affect the alignment of motors windings, causing further complications in the repair. If these issues are not addressed, the electric motor isn't likely to function effectively and could lead to more extensive repairs.
What factors should be considered in dc electric motor repair to prevent issues related to motor resist and ensure the motor housing gets the proper treatment especially in relation to worn bearings cause?
When performing dc electric motor repair, it is crucial to consider factors such as the condition of the motor resist and the proper care of the motor housing to prevent problems. Ensuring that worn bearings cause minimal disruption will help maintain the efficiency and longevity of the motor during the repair process.
How can proper treatment of the motor housing get impacted during dc electric motor repair?
During dc electric motor repair, ensuring that the motor housing gets the proper treatment is crucial. If the motor housing does not receive adequate attention, it can lead to misalignment, overheating, and other issues that may affect the overall performance of the motor. It's essential to inspect the motor housing thoroughly and apply protective measures to ensure its longevity and functionality during the repair process.