How to troubleshoot an electric motor?
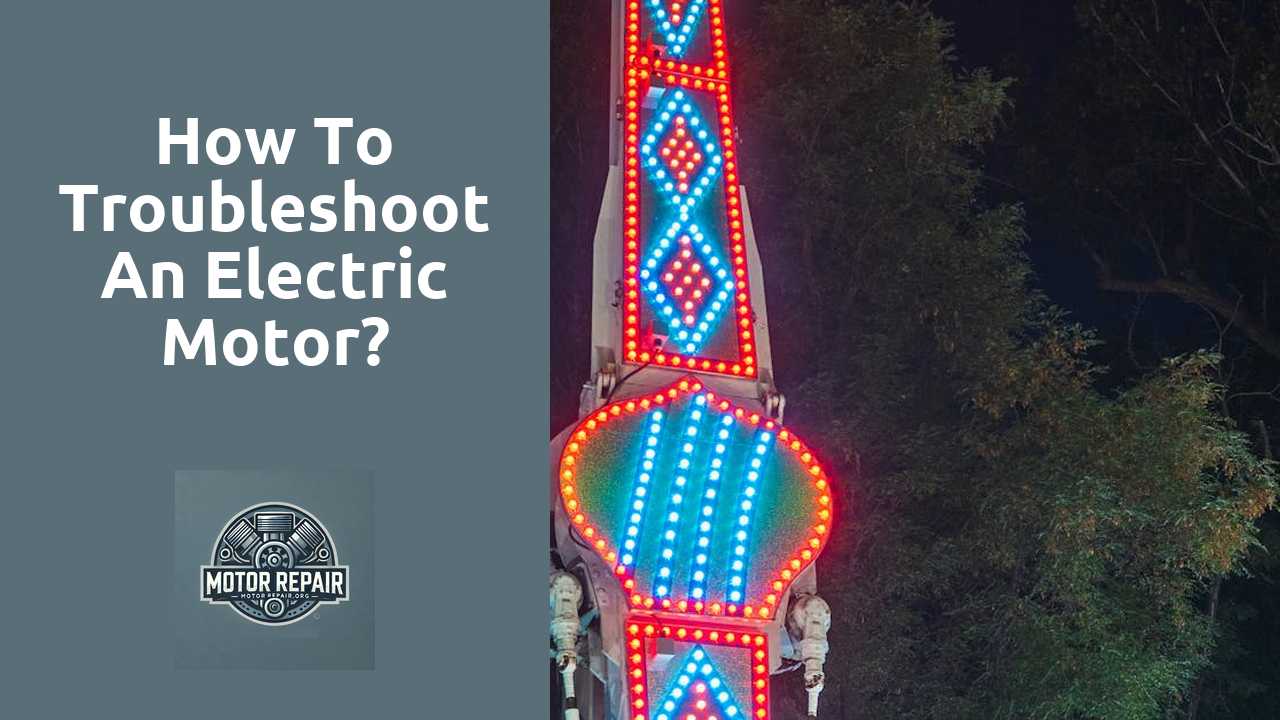
Table Of Contents
Checking Electrical Connections
A reliable electric motor begins with secure electrical connections. Loose or corroded connections can disrupt the flow of electricity and lead to performance issues. Start by inspecting all connecting hardware, ensuring that terminals are tight and free from rust or debris. Pay special attention to any connectors that exhibit signs of wear or damage, as these could be the source of the problem.
Perform a visual check to identify any frayed or damaged wires. Damaged insulation can expose conductors and create a risk of short circuits. If any issues are found, replace the damaged wires promptly. It may also be beneficial to apply dielectric grease to connections to prevent corrosion in the future. Maintaining clear and clean electrical connections is vital for ensuring the efficient operation of the motor.
Discover more here.
Testing Wires and Terminals
Ensuring the integrity of wires and terminals is crucial in diagnosing issues with an electric motor. Start by visually inspecting the wiring for signs of wear, abrasions, or corrosion. Check connections to make sure they are secure and free of dirt or debris. Loose or damaged terminals can lead to intermittent connections that disrupt motor function.
Utilizing a multimeter can help assess the condition of wires. Set the multimeter to the resistance setting and measure the impedance across various wire segments. High resistance readings may indicate damage or breaks in the wire. Additionally, test terminals for both continuity and secure connections to ensure that energy flows correctly through the system.
Measuring Voltage and Current
Accurate measurement of voltage and current is crucial for diagnosing electrical issues in a motor. Begin by utilizing a multimeter to check the supply voltage at the motor terminals. It is essential to ensure that the voltage matches the specifications listed on the motor's nameplate, as deviations could indicate underlying problems. Testing current draw while the motor is running offers insight into its operating condition. A motor that draws too much current may be suffering from mechanical issues, whereas low current could signify problems such as a lack of load or internal faults.
When measuring voltage and current, adhere to safety protocols to prevent accidents. Always ensure that the multimeter settings are appropriate for the type of measurement being taken. For voltage, set it to the alternating current (AC) or direct current (DC) mode as needed. For current, choose the correct amperage range to avoid damaging the meter. Careful note of the readings, along with comparisons to the manufacturer's specifications, will contribute to a thorough analysis of the motor's electrical health.
Techniques for Accurate Readings
Ensuring accurate voltage and current measurements is vital for effective troubleshooting of electric motors. Utilizing a digital multimeter allows for precise readings. It is crucial to set the multimeter properly before taking measurements. For voltage, the device should be adjusted to the appropriate AC or DC setting based on the motor specifications. For current measurements, using a clamp meter can prevent the need to break the circuit, reducing the risk of errors and potential hazards.
Calibration of testing equipment plays an essential role in achieving reliable results. Regularly checking the accuracy of your multimeter or other devices protects against misleading readings. Additionally, always ensure that connections are secure during testing to avoid fluctuations in data. Conducting tests during peak load conditions can uncover performance issues that might not be evident during idle states. These practices contribute to a thorough analysis, allowing for informed decisions about motor repairs or replacements.
Motor Performance Testing
Assessing the performance of an electric motor involves several key factors, including speed and efficiency. Various testing methods can be employed to gather data on how well the motor operates under different loads. This might include monitoring the motor’s RPM to ensure it meets manufacturer specifications. Testing ensures the motor runs as intended and highlights any discrepancies that may indicate underlying issues.
Efficiency can be gauged by measuring input power versus output power. This can be accomplished through the use of specialized instruments that provide insights into the motor's overall performance. Observing the temperature during operation is also crucial, as excessive heat may signify friction or electrical issues. Together, these evaluations offer a comprehensive view of the motor's health and ability to perform optimally.
Evaluating Speed and Efficiency
Assessing the speed and efficiency of an electric motor is crucial for understanding its performance. This can be achieved through tachometers, which measure rotational speed in revolutions per minute (RPM). A motor running below its specified RPM can indicate issues such as excessive load or electrical problems. Additionally, monitoring the motor's efficiency—defined as the ratio of output mechanical power to input electrical power—provides insights into potential energy losses within the system.
Another method to evaluate performance involves conducting a load test. This process determines how well the motor operates under varying loads. Observing parameters like temperature and vibration can also reveal performance issues. Consistent high temperatures may suggest that the motor is overworking, while irregular vibrations can indicate mechanical faults. Regular evaluations like these help ensure optimal operation and longevity of the motor.
FAQS
What are the first steps to troubleshoot an electric motor?
The first steps to troubleshoot an electric motor include checking the electrical connections, inspecting wires and terminals for damage, and ensuring that power is reaching the motor.
How can I test the wires and terminals of an electric motor?
You can test the wires and terminals by using a multimeter to check for continuity and resistance. Look for any signs of wear or corrosion, and ensure that all connections are secure.
What is the importance of measuring voltage and current in troubleshooting a motor?
Measuring voltage and current is crucial because it helps determine whether the motor is receiving the correct power supply. It can also reveal issues such as overloads or shorts that may be affecting performance.
What techniques can I use for accurate voltage and current readings?
To ensure accurate voltage and current readings, use a properly calibrated multimeter, avoid measuring under load if possible, and take multiple readings to confirm consistency.
How can I evaluate the speed and efficiency of an electric motor?
You can evaluate the speed of an electric motor using a tachometer, while efficiency can be assessed by comparing input power to output power, taking into account the motor's load conditions during operation.
Related Links
electric motor repairIs it worth repairing an electric motor?
Can a small electric motor be repaired?
What are the three most common electrical problems in an electric motor?