Essential Guide to Motor Rewinding: Understanding Electric Motor Rewind Techniques and Sales
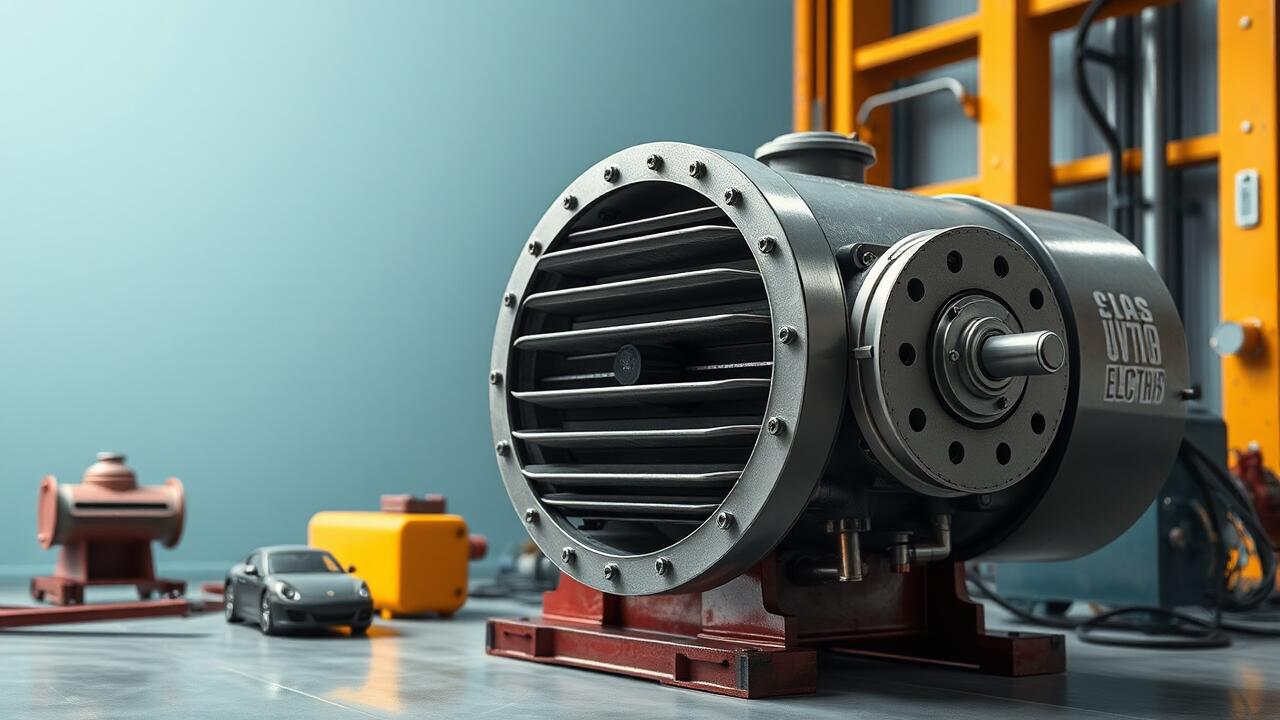
Table Of Contents
Key Takeaways
- Grasping the concept of motor rewinding
- The procedure involved in rewinding motors
- Frequent problems associated with motors
- The significance of expert assistance
Understanding Motor Rewinding
Motor rewinding is a crucial maintenance process for various types of motors, including AC motors, DC motors, and three-phase electric motors. This procedure involves replacing the worn-out windings of an electric motor to restore its motor function effectively. A properly executed motor rewinding can significantly extend the lifespan of electric motors, such as hazardous location motors, asynchronous motors or three-phase motors, by ensuring optimal performance. Techniques and tools used in motor rewinding vary, catering to the specific requirements of different motor types, whether they be a DC motor or an asynchronous electric motor. Understanding the significance of motor rewinding helps in recognizing the need for timely intervention, ensuring that any issues affecting an electrical motor are promptly addressed.
What is Motor Rewinding?
Motor rewinding involves the process of refurbishing electric motors, specifically focusing on the windings of the rotor and stator. This procedure is essential for maintaining the functionality of various types of motors, including AC motors and servo motors. As windings degrade over time due to wear and tear, they can lead to increased winding resistances that affect overall motor performance. A thorough inspection often accompanies this process, examining components such as bearings and conducting vibration analysis to identify any underlying issues that may not be immediately visible.
The importance of understanding motor rewinding lies in its ability to restore machines to optimal speed and performance levels. By replacing damaged windings, technicians can significantly reduce vibration and enhance the efficiency of the motor. The rewinding process ensures that rotors operate harmoniously within the stator, promoting longevity and reliability. Properly executed motor rewinding is a crucial aspect of motor maintenance, allowing for the uninterrupted operation of essential machinery.
Benefits of Motor Rewind
Motor rewinding offers significant advantages for maintaining and enhancing the performance of electric motors. A successful rewind motor restores the integrity of the coils, which is crucial for achieving optimal rotation speed. By replacing damaged or worn insulation and wiring, efficient motor rewinding helps to ensure that the voltage supplied to the motor meets its operational requirements. This process can ultimately lead to increased power output, reduced energy consumption, and a longer lifespan for the motor.
Investing in a comprehensive motor rewind can greatly reduce the likelihood of unexpected downtimes. With needed motor rewinding, the potential for overheating and electrical failures diminishes significantly. A well-executed motor rewind process revitalizes the motor, improving its efficiency and reducing operational costs. As a result, industrial operations can maintain productivity and minimize maintenance expenditures, demonstrating the importance of proper motor rewinding practices.
The Motor Rewind Process
Motor winding repair involves a series of methodical steps designed to restore the efficiency and functionality of an electric motor. Understanding the motor rewinding requirements is crucial for achieving a straightforward motor rewind. Technicians begin by disassembling the motor to detect any existing motor issues and assess the condition of the windings. After removing the damaged winding, they replace it with new wire, tailored to the motor's specific application. Once rewound, the motor must be meticulously reassembled to ensure optimal performance. A professional motor rewind guarantees that the rewound electric motor meets industry standards, thereby preventing additional motor issues in the future. By turning the motor back into service efficiently, businesses can minimize downtime and enhance productivity.
Steps Involved in Rewinding an Electric Motor
The process of motor rewinding begins with the careful disassembly of the entire motor to access the electric motor windings. This initial step is crucial for identifying any motor problems that may be contributing to decreased motor performance. Assessing the condition of the motor components allows technicians to determine whether a replacement motor is needed or if the current used motor can be salvaged. As the windings are removed, technicians take note of the motor connection setup to ensure accurate reinstallation.
After the windings have been extracted, the next phase involves measuring and replacing the wire in accordance with the specifications for the specific motor. This step plays a significant role in restoring motor efficiency and optimizing motor speed. Once the new windings are installed, technicians reassemble the motor, ensuring that all parts fit together seamlessly. Proper reassembly directly impacts the overall motor performance and minimizes the risk of future motor failures, ultimately extending the lifespan of the electric motor.
Tools and Equipment Needed for Motor Rewind
Successful motor rewinding requires a specific set of tools and equipment tailored to the motor's construction and design. A technician might need to disassemble the motor carefully, ensuring that all components are preserved for analysis later. Equipment such as winding machines, insulation testers, and soldering tools are essential in executing effective rewinds. For phase motors, specialized tools may be necessary to ensure that the rewinding process meets the desired motor performance standards.
Choosing the right tools significantly impacts the quality of the motor repair and the longevity of the newly rewound motor. Having the appropriate instruments helps technicians execute rewinds with precision and confidence. Properly analyzing the old motor rewound can reveal insights into the overall motor design, guiding the technician in delivering optimal motor services. Neglecting to gather the necessary equipment can lead to a lengthy motor replacement or subpar performance following a rewind.
- Winding machines for accurate coil formation
- Insulation testers to check for electrical integrity
- Soldering tools for secure connections
- Digital multimeters for measuring voltage and resistance
- Torque wrenches for securing motor components
- Heat guns for applying heat shrink tubing
- Cleaning supplies to maintain component condition
Common Motor Issues
Identifying issues that require motor rewinding is crucial in maintaining the efficiency of an electric motor. An old motor may exhibit symptoms such as unusual noises, overheating, or decreased performance, indicating potential problems with the motor coils or other internal components. Professional motor services often involve a thorough test motor process, allowing technicians to diagnose issues accurately. Many motor manufacturers offer comprehensive motor solutions, including assessments to determine whether a successful rewind is necessary. In a well-equipped motor shop, skilled professionals perform rewindings with precision, ensuring that the motor terminal connections are secure and functioning correctly. Regular electric motor maintenance can prevent more significant issues from arising, promoting longevity and reliability in your electric motor system.
Identifying Problems That Require Motor Rewind
Signs of motor problems can often signal the necessity for motor rewinding. Inexpensive motor models, particularly screw motors and pole motors, might show wear that requires immediate attention. Common issues include overheating, unusual noises, or fluctuations in motors speed. Such symptoms can indicate an impending complete motor failure, pinpointing the need for an electrical motor repair. Quick intervention through the rewind process can often extend the lifespan of different motors, ensuring they operate at optimal efficiency.
Recognizing the signs early can save costs related to new motor sales. Electric motor service providers often emphasize the importance of addressing minor issues before they escalate. The rewinding process, if executed with quality motor repair standards, can restore functionality to motors that might otherwise be deemed unserviceable. Identifying the right moment for motor rewinding can significantly affect the overall performance and reliability of the machinery involved.
Preventative Maintenance to Avoid Motor Downtime
Regular preventative maintenance is crucial for extending the lifespan of electric motors. By routinely inspecting motor coils and ensuring proper motor insulation, potential problems can be identified early. This proactive approach significantly reduces the risk of rotor losses and common issues that might lead to motor rewinding. Maintaining the integrity of the motor housing also protects against environmental damage, which can affect industrial motors and A/C motors alike.
Scheduling professional motor service can save time and reduce costs associated with unplanned downtime. Experts can perform detailed assessments and implement maintenance strategies tailored to specific motor needs. Upgrading to new motors or utilizing VPI style motor insulation can also enhance overall electric motors performance. Addressing minor issues before they escalate into major failures ensures the reliability of motors, allowing industrial operations to continue smoothly.
The Importance of Professional Service
Seeking expert help for motor rewinding is crucial to ensure the longevity and efficiency of your electric motor. Professionals possess the knowledge to assess various motors specifications, including small motors and green motors, and determine whether they require new windings, replacement windings, or repairs to faulty windings. They apply appropriate techniques to restore electric motor insulation, particularly when dealing with locked rotor situations or single-phase motors. Experienced technicians utilize methods like motor VPI stator treatment to enhance the durability of electrical windings. Timely winding and precise reassembly contribute significantly to preventing premature motor failure, ensuring optimal performance for years to come.
- Professional service leads to better diagnosis of motor issues.
- Expert technicians have access to specialized tools and equipment.
- Quality repairs can save costs in the long term by extending motor life.
- Ensures compliance with industry standards and regulations.
- Regular professional maintenance can improve energy efficiency.
- Professionals can provide valuable advice for proper motor care.
- Quick turnaround times can minimize downtime for your operations.
When to Seek Expert Help for Motor Rewinding
Expert assistance becomes crucial for motor rewinding when motors display signs of severe wear. Old windings and worn bearings can compromise the efficiency of mechanical devices, leading to reduced performance and potential failure. If the original windings show significant deterioration or if there is a need for a new winding that adheres to the original winding pattern, professionals are equipped to ensure the appropriate winding design is implemented. Their expertise allows for a meticulous rewinding process that guarantees long-lasting results.
The need for expert help also arises during the reassembly phase. Professionals possess the skills necessary for installing new bearings, replacing or repairing components, and ensuring the last windings match the specifications of the original windings. This attention to detail not only enhances the durability of the rewound motor but also minimizes the risk of future issues. Seeking professional help can save time and resources by ensuring that the motor is restored to optimal working condition.
How Professionals Reassemble Motors After Rewinding
The reassembly of motors after motor rewinding requires precision and expertise. Technicians begin by carefully placing coils back into the stator windings, following the necessary winding pattern to ensure proper functionality. Tools specifically designed for winding help professionals achieve the correct winding factor. Throughout this winding process, the use of an automated coil machine may be employed for layer winding, ensuring each layer is evenly spaced and secured. This equipment can often enhance productivity and accuracy during the reassembly.
After the coils are in place, the next step involves coil vibrating to eliminate any potential shorted turn-to-turn issues. This step is critical to maintaining the integrity and durability of the motor. Professionals monitor the speeds during this phase to ensure that the winding has settled correctly without causing damage. Finally, technicians utilize specialized winding tools to secure everything in place before testing the motor's performance post-rewinding. Each of these steps is vital to restore the motor’s efficiency and longevity.
Conclusion
Motor rewinding serves as a critical restoration technique for electric motors, helping to extend their lifespan and improve efficiency. Detailed analysis of winding data assists technicians in identifying the condition of both spent windings and non-varnished coil windings, ensuring that replacements are precisely tailored to the motor’s specifications. The efficiency of air compressor repairs often hinges on successful motor rewinding, as it addresses losses incurred from degraded coils. Regular cycles of maintenance and rewinding can significantly mitigate potential downtimes, promoting optimal performance in advanced air systems. Understanding each element of this process is essential for anyone looking to maintain the integrity of their motor systems.
FAQS
What is motor rewinding?
Motor rewinding is the process of replacing the worn or damaged winding coils of an electric motor to restore its functionality and efficiency.
Why should I consider motor rewinding?
Motor rewinding can extend the life of your motor, improve its performance, and is often more cost-effective than purchasing a new motor.
How can I identify if my motor needs rewinding?
Common signs include unusual noises, overheating, reduced performance, or frequent tripping of the circuit breaker.
What tools are needed for motor rewinding?
Essential tools include a multimeter, winding jig, soldering iron, insulation materials, and winding tools.
How long does the motor rewinding process usually take?
The duration can vary depending on the complexity of the motor and the extent of damage, but it typically ranges from a few hours to several days.
What are the common issues that can occur during an electric motor rewind process for a three phase motor?
When performing electric motor rewinding, particularly with three phase electric motors, it is essential to carefully analyze motor construction to identify common issues that may arise. These can include motor insulation failures, which often lead to premature motor failure if not addressed. During electric motor rewinds, the winding head must support careful placement of coils to ensure the motor functions correctly. A thorough understanding of motor applications and construction can help prevent these common issues and ensure a successful motor rewinding process.
How can one ensure a successful rewind of a three phase motor and what common issues can arise during the process?
Ensuring a successful rewind of a three phase motor involves careful analysis of the motor before starting the rewinding process. The electric motor refers to careful disassembly of the motor components to access the motors coils properly. It's crucial to note the colour form motor wiring for accurate replacement. Common issues that motors experience during this process can include misalignment of coils, which can prevent premature motor failure, and timing during winding, which enables motors to operate efficiently. By taking the time to carefully place coils and examining how the motor depends on proper winding techniques, one can substantially reduce potential risks associated with electric motor repairs.
How should one approach the process to turn a motor and analyse motor faults before performing a rewind?
To turn the motor and analyze motor faults effectively, it's important to first disassemble the motor carefully. This involves inspecting for common issues motors may have, assessing the winding condition, and determining the necessary time winding for repairs. Additionally, implementing green winding techniques ensures that coils are placed in a careful manner to prevent future issues.
What steps need to be taken to properly turn a motor and disassemble the motor before rewinding it?
To properly turn the motor, you should first ensure that you have the right tools on hand. Begin by carefully disassembling the motor, noting the arrangement of parts for reassembly. When you disassemble the motor, it's important to carefully place coils and other components in a safe location to prevent damage, allowing for a smooth rewind process.
What is the best method to turn a motor and disassemble the motor while ensuring that you have a careful place for the coils?
To turn the motor effectively, start by securing it in a stable position to avoid any movement. When disassembling the motor, follow the manufacturer's guidelines to keep parts organized. It's crucial to keep the coils in a careful place to prevent damage and facilitate easier rewinding later.
How can I effectively turn a motor and disassemble the motor while also ensuring I have a careful place for the coils during the rewind process?
To effectively turn the motor, you should first ensure it is securely mounted, then use appropriate tools to carefully disassemble the motor. While disassembling, it’s essential to have a careful place for the coils to avoid any damage. Organizing the components as you remove them will aid in the rewind process later on.
What precautions should be taken when you turn a motor and disassemble the motor to ensure that there is a careful place for the coils?
When you turn the motor and disassemble the motor for a rewind, it’s crucial to create a careful place for the coils to prevent damage. Use clean, padded surfaces to lay the coils down safely. Ensure you label each coil and its position to facilitate accurate reinstallation. Maintain organization during the process to avoid confusion and potential mistakes.
What strategies can I implement to effectively turn a motor and disassemble the motor while ensuring a careful place for the coils?
To effectively turn the motor and disassemble the motor, it is crucial to use appropriate tools and techniques that minimize movement and wear. Make sure to label all components as you disassemble the motor to keep track of them. Additionally, establish a careful place for the coils, such as using a padded surface or organizing bins to prevent damage during the rewind process.
What strategies can help in organizing a careful place for the coils when you turn the motor and disassemble the motor for a rewind?
To efficiently turn the motor and disassemble the motor while ensuring a careful place for the coils, you should prepare a designated workspace that is clean and free of clutter. Use labeled containers to store the coils and parts as you disassemble the motor, and keep the coils organized to prevent any damage. Additionally, take photos during the disassembly process to make reassembly easier.
What is the importance of having a careful place for coils when you turn the motor and disassemble the motor for rewinding?
Having a careful place for the coils when you turn the motor and disassemble the motor is crucial because it prevents damage to the coils and helps maintain organization. Properly managing the coils in a designated area ensures that they are not tangled or misplaced, facilitating a smoother rewind process and reducing the risk of errors.