Expert Guide to MG Set Repair: Tips and Techniques for Efficient Restoration
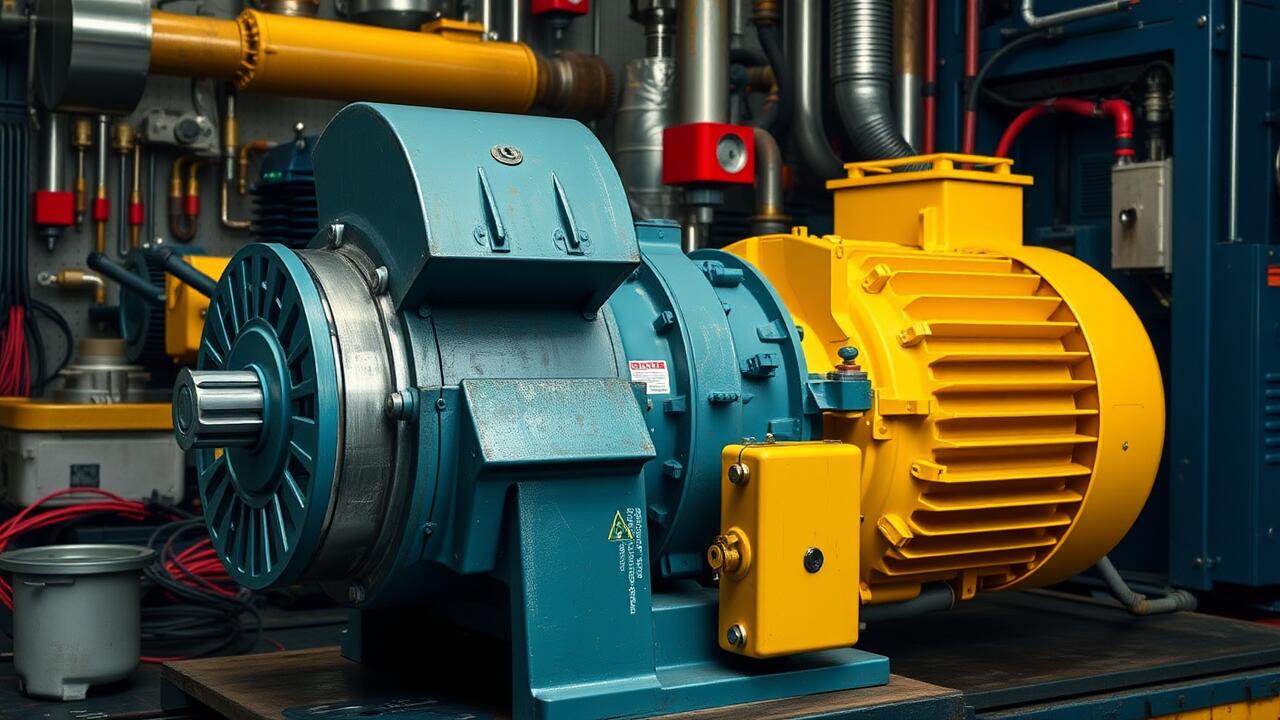
Table Of Contents
Key Takeaways
- Comprehending MG Set Restoration
- Significance of Prompt Fixes
- Instruments and Gear for MG Set Restoration
- Methodical Approach to MG Set Restoration
- Proactive Care Suggestions for MG Sets
Understanding MG Set Repair
MG sets, or motor-generator sets, are crucial in providing reliable power through their mechanical systems. Routine maintenance and repair are essential to ensure their longevity and efficiency. Common components that may require attention include the battery and various mechanical parts, which can be made from materials such as stainless steel for enhanced durability. Understanding the nuances of mg set repair involves recognizing potential issues early, conducting thorough inspections, and performing timely repairs. By focusing on these aspects, operators can significantly reduce downtime and improve the overall performance of their generator sets.
What Are MG Sets?
MG sets, or Motor Generator sets, are essential machines that convert mechanical energy into electrical energy. These systems typically consist of various components, including coils, pumps, and iron structures that support their operation. Proper functionality of these machines is critical for many industrial applications, making MG set repair a priority when issues arise. The combination of high-performance pumps and motors ensures that power generation remains efficient, but wear and tear can lead to significant challenges.
Understanding the intricacies of MG sets is vital for anyone involved in their maintenance or repair. A machine shop equipped with the right tools can address problems related to both electrical and mechanical components. Regular mg set repair is crucial to maintaining optimal performance, as even minor issues can escalate into major operational failures. By focusing on the components such as coils and pumps, technicians can effectively troubleshoot and restore these vital machines to working condition.
Common Issues Faced by MG Sets
MG sets frequently encounter issues that can impede their efficiency. A common problem arises from wear and tear of cast iron components, which can lead to mechanical failures. Regular mg set repair is essential to address these concerns before they exacerbate. Lack of proper lubricant application can also cause friction-related malfunctions, resulting in frequent breakdowns. Using the right tools to detect these issues early on can significantly prolong the life of the machine.
Voltage irregularities often present another challenge for MG sets. Fluctuations in voltage can affect the overall performance and reliability of the equipment. Routine mg set repair can help identify the source of voltage problems, ensuring that the electrical system functions correctly. Technicians must employ specific tools designed for measuring voltage levels and diagnosing electrical faults. Addressing these common problems proactively not only improves machine efficiency but also minimizes the risk of costly repairs in the future.
- Regularly inspect cast iron components for signs of wear and tear.
- Ensure proper lubrication is applied to reduce friction and prevent breakdowns.
- Use diagnostic tools to detect issues early and address them promptly.
- Monitor voltage levels routinely to catch fluctuations before they escalate.
- Schedule periodic maintenance checks to identify and resolve potential problems.
- Train staff on best practices for operation and maintenance of MG sets.
- Keep a log of repairs and maintenance activities to track performance trends.
The Importance of Timely Repairs
Timely mg set repair plays a crucial role in maintaining the efficiency and longevity of mg sets. Delaying repairs can lead to complications that not only escalate repair costs but also jeopardize the performance of the generator. A well-executed repair project within a qualified repair facility ensures that the mg set operates optimally, preventing potential failures during critical operations. Regular generator repair helps to identify underlying issues early, allowing for comprehensive maintenance and reducing downtime. Addressing problems promptly not only enhances the reliability of the mg set but also extends its lifespan, ensuring that it continues to meet operational demands effectively.
Consequences of Neglecting Maintenance
Neglecting maintenance on MG sets can lead to significant issues that escalate repair costs and downtime. Frequent breakdowns may necessitate more extensive in-shop generator repair or portable generator repair, putting additional pressure on the repair space. Routine maintenance helps detect minor faults before they develop into major problems, potentially saving time and resources on comprehensive machine tool repair or multi-stage pump repair.
A lack of regular upkeep can result in inefficient operation, leading to increased energy consumption and reduced performance. Failing to address these issues may eventually require the MG set to be sent to a specialized repair center, which could disrupt operations and impact productivity. Prioritizing MG set repair ensures systems run reliably, minimizing the risk of costly repairs at inconvenient times.
Benefits of Prompt MG Set Repair
Timely motor generator set repair can significantly enhance the efficiency and longevity of the equipment. Addressing repair needs promptly prevents minor issues from escalating into major mechanical failures. Regular maintenance, such as booster pump repair or gearbox repair, can minimize downtime and reduce operational costs. For instance, a neglected lewis motor repair might result in complete motor generator failure, which could lead to costly replacements and extensive downtime.
Prompt repairs also ensure the safety of the operating environment. Mechanical repairs that are deferred can pose risks not just to the equipment but also to personnel. Engaging in timely mg set repair helps maintain optimal performance levels, which is crucial in preventing accidents. Addressing problems like repair motor generator issues swiftly safeguards against more severe complications and ensures smooth operation of all machinery involved.
Tools and Equipment for MG Set Repair
Essential tools and equipment play a pivotal role in effective mg set repair, especially within the confines of an in-shop repair setting. Repair departments are often equipped with specialized instruments tailored for specific tasks, such as motor part repair and circulation pump repair. Motor repair specialists rely on these tools to diagnose and address various issues, including those associated with emx motor repair. Each tool serves a unique purpose, ensuring that every aspect of mg set repair is executed with precision and efficiency. The right tools not only enhance the repair process but also contribute to the longevity and performance of the equipment.
Essential Tools for Diagnosing Issues
Diagnosing issues in MG sets requires a variety of specialized tools to ensure accuracy and efficiency in the repair process. Equipment such as multimeters, oscilloscopes, and clamp meters are essential for diagnosing electrical faults. These tools not only help in identifying problems but also streamline the troubleshooting phase, making them invaluable for mg set repair. For more extensive issues like those found in hvac sensors , pump repair or electric motor repair, advanced diagnostic tools may be necessary to conduct thorough evaluations.
It is crucial to have access to reliable resources for top-notch repair services, which often include electronic repair services. Utilizing appropriate tools during shop repairs enhances the likelihood of identifying all potential faults. For instance, specialized equipment is critical for cryogenic shaft installation tasks and ensuring that repairs are completed accurately and efficiently. Proper diagnostics not only expedite the mg set repair process but also contribute to the overall longevity and performance of the machinery.
Safety Equipment Required for Repairs
Proper safety equipment is crucial during mg set repair to ensure the safety of technicians and the integrity of the equipment being worked on. Essential gear includes gloves and goggles to protect against electrical shocks and mechanical injuries during specific repairs. Adequate footwear is also important, particularly when performing small motor repair or submersible pump repair, as these tasks often involve working in potentially hazardous environments.
Having the right tools and protective equipment enhances the effectiveness of repair services. Harnesses and fall protection gear are necessary for any overhead work, especially with complex mechanical operations. Using insulated tools during electrical repair can prevent accidents. This combination of safety equipment allows technicians to focus on fixings and repairs without the added concern of personal safety.
Step-by-Step Guide to MG Set Repair
A comprehensive approach to MG set repair involves several crucial steps aimed at ensuring efficiency and lasting performance. The initial inspection process plays a vital role in identifying issues, whether it involves grinder pump repair or exciter repair. Common problems often relate to worn-out components requiring collector ring replacement or general motor repair. Conducting thorough diagnostics at this stage helps in planning for long-lasting repairs, ultimately benefiting the motor repair business. This systematic guide ensures that all necessary repairs are executed effectively, enhancing the reliability of MG sets.
- Conduct a detailed initial inspection of the MG set components.
- Identify any worn-out or malfunctioning parts that may need repair or replacement.
- Perform diagnostics to determine the root cause of any identified issues.
- Plan and gather necessary materials and tools for the repair process.
- Execute repairs systematically, starting from the most critical components.
- Test the repaired MG set to ensure optimal performance and efficiency.
- Document the repairs and outcomes for future reference and maintenance planning.
Initial Inspection Process
Performing an effective initial inspection is crucial for successful mg set repair. Technicians should start by examining the mechanical parts thoroughly, paying close attention to common issues like defective rotor bars and faulty equipment. This stage often involves checking the alignment of the shaft modifications and ensuring all components are functioning as intended. Identifying potential problems early can significantly streamline the repair process and prevent further damage to the equipment.
During the inspection, it is essential to assess the functionality of the generator repair ips. Any signs of wear or malfunction can point to underlying issues requiring in-house motor repair. A comprehensive evaluation not only helps in diagnosing current problems but also aids in anticipating future maintenance needs. Consistent attention to these details can enhance the longevity and efficiency of the mg set, reducing the risk of unexpected breakdowns.
Troubleshooting Common Problems
Identifying issues in MG sets often requires a systematic approach to troubleshooting. Begin by assessing the overall electrical equipment condition, focusing on components integral to function and safety. Look for signs of coil damage, which can significantly impact performance. Small motor repairs may be necessary if the motors are not running smoothly. Regular checks can prevent minor issues from escalating into major failures, thereby facilitating more accessible mg set repair processes.
Flow pump repair and fire pump repair may also come into play during the troubleshooting phase. Inspecting these components can help diagnose power supply issues that could affect the entire MG set's operation. Addressing problems early on leads to more efficient electric motor repairs, ensuring the system operates optimally. A thorough investigation into any irregularities is crucial for maintaining reliable function in MG sets.
Performing Electrical Repairs
Electrical repairs for MG sets require a methodical approach to ensure optimal performance. Identifying pump problems or issues with the mechanical components is essential before proceeding. A thorough check of sensitive equipment and connections can highlight areas needing attention. Utilizing specialized tools for MG set repair can facilitate expert repairs and increase overall efficiency.
After diagnosing the issues, careful attention must be given during the actual repair process. Proper techniques in welder repair and electrical adjustments ensure that all components function harmoniously. Ensuring that mechanical equipment monitoring is in place can help prevent future setbacks and prolong the life of the MG set. Prioritizing safety and accuracy during these repairs will lead to better operational reliability.
Preventive Maintenance Tips for MG Sets
Routine inspection is crucial for maintaining the efficiency of MG sets. Regularly conducting collector ring inspections can help identify electrical issues early, reducing the need for extensive mg set repair later. Focus should also be placed on the condition of shaft extensions and the bearings, as worn components can lead to significant operational disruptions. Installing bearings at recommended intervals reduces friction and wear, promoting optimal performance. Keeping a detailed log of repairs and replaced parts ensures that all maintenance actions are tracked, facilitating better decision-making for future mg set repair needs. Regular checks on the shaft and associated components can prevent minor issues from escalating into major problems.
Routine Inspection Checklist
Regular inspections are crucial for the effective operation of MG sets. This process involves checking essential components such as the equipment, shafts, and electrical systems. Identifying wear and tear early can prevent major issues, making it easier and more cost-effective to perform mg set repair. Keeping a detailed log of inspection results helps in tracking performance and any recurring problems.
The inspection checklist should include key areas such as fluid levels, belt conditions, and electrical connections. Pay attention to any unusual noises or vibrations during operation as these could indicate potential failures. Implementing this routine not only extends the life of the equipment but also minimizes the need for emergency mg set repair, ensuring that the system runs smoothly and efficiently.
Conclusion
MG set repair is essential for maintaining the efficiency and longevity of mechanical systems. Addressing repair needs promptly can prevent minor issues from escalating into major problems, such as those related to booster pump repair or gear box repair. Regular maintenance and timely repairs, including repair motor generator tasks and specialized services like Lewis motor repair, ensure that all components function optimally. Without proper attention, mechanical repairs may become more complex and costly, leading to extended downtime and potential operational losses. Consistent care and adherence to a routine inspection checklist will safeguard the performance of MG sets for years to come.
FAQS
What is an MG set?
An MG set, or motor-generator set, is a combination of an electric motor and a generator used to convert mechanical energy into electrical energy. It is commonly used for various applications, including backup power supplies and voltage regulation.
What are common issues faced by MG sets?
Common issues with MG sets include electrical failures, mechanical wear and tear, overheating, fuel system problems, and irregular vibrations. Regular maintenance can help prevent these issues.
Why is timely repair of MG sets important?
Timely repair of MG sets is crucial to prevent further damage, ensure reliable operation, and avoid costly downtime. It helps in maintaining efficiency and safety, especially in critical applications.
What tools are essential for MG set repair?
Essential tools for MG set repair include multimeters for electrical diagnostics, wrenches and screwdrivers for mechanical repairs, and specialized equipment like oscilloscopes for troubleshooting electrical issues.
How can I perform preventive maintenance on my MG set?
Preventive maintenance on your MG set includes routine inspections, checking fluid levels, cleaning filters, tightening loose connections, and replacing worn-out parts. Following a regular maintenance schedule can extend the lifespan of the set.
What are the key steps to consider when performing a mg set repair?
When performing a mg set repair, it is important to follow vital steps such as diagnosing the issue, gathering necessary tools, turning off the power supply, inspecting components, and replacing any faulty parts to ensure a thorough and effective repair process.
What tools are necessary for a successful mg set repair?
To successfully perform an mg set repair, it is essential to have the right tools at your disposal. Common tools include wrenches, screwdrivers, multimeters, and diagnostic equipment. Depending on the specific issue, you may also need replacement parts like filters, belts, and gaskets to ensure the repair is effective and the mg set operates smoothly afterward.
How can I ensure the longevity of my mg set before it requires repair?
To ensure the longevity of your mg set and minimize the need for repair, it's important to follow a regular maintenance routine, including checking and changing oil, ensuring proper cooling, and inspecting electrical connections.
How do environmental factors influence the need for mg set repair?
Environmental factors, such as extreme temperatures, humidity, and exposure to dust and debris, can significantly impact the performance of a mg set. These conditions may lead to more frequent issues that necessitate repair, highlighting the importance of regular maintenance and monitoring to ensure the set operates efficiently.
What are the most common issues that require mg set repair?
The most common issues that require mg set repair include mechanical failures, electrical faults, fuel system problems, and wear and tear on components. Regular inspection and maintenance can help identify these issues early, ensuring the mg set operates efficiently and reducing the frequency of repairs.