Comprehensive Guide to Industrial Motor Repair and Electric Motor Solutions
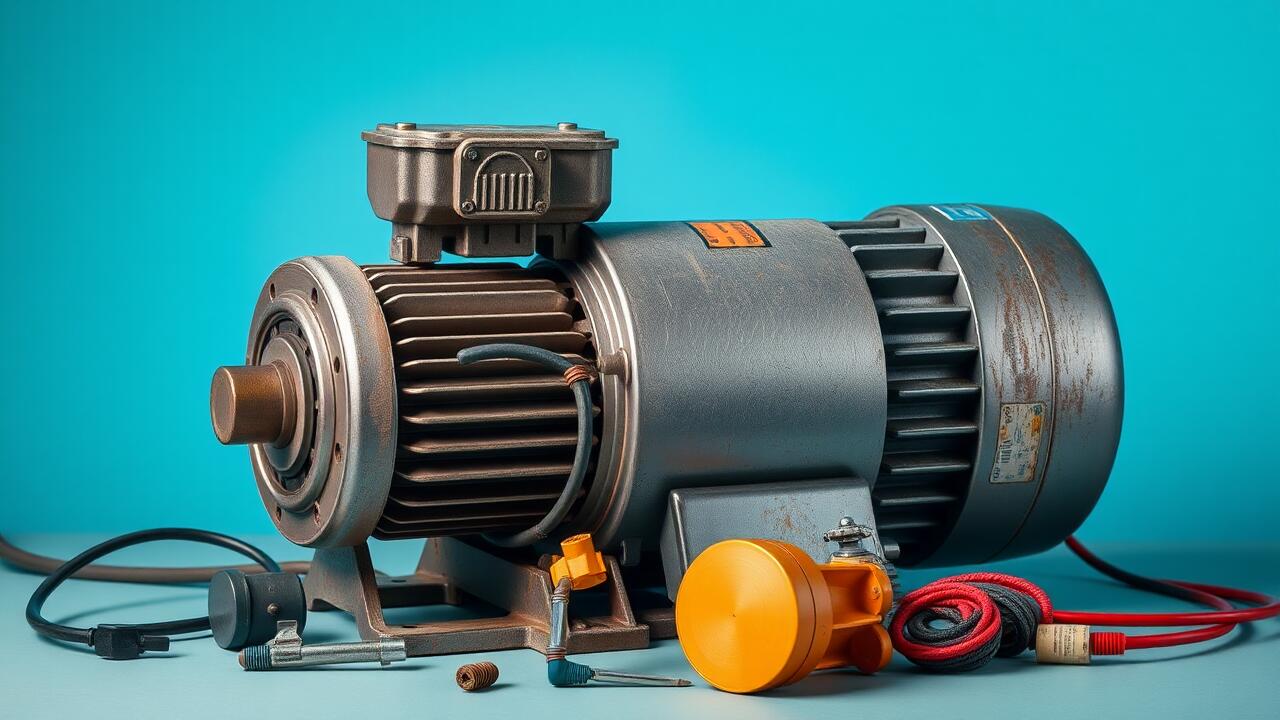
Table Of Contents
Key Takeaways
- Comprehension of industrial motor restoration
- Varieties of electric motor refurbishment
- Recognizing industrial motor requirements
- The restoration procedure for industrial motors
- Optimal strategies for spare motor upkeep
- Choosing a qualified repair service
Understanding Industrial Motor Repair
Timely industrial motor repair is crucial for ensuring the longevity and efficiency of electric motors used in various industrial applications. Regular maintenance and repair can prevent extensive damage and reduce downtime associated with malfunctioning motors. A comprehensive understanding of motor control systems, including both AC and DC motor technologies, is vital for identifying issues early. By recognizing common problems and implementing effective repair and maintenance strategies, facilities can enhance their operational efficiency. This proactive approach not only extends the life of the motors but also supports overall productivity in the industrial sector.
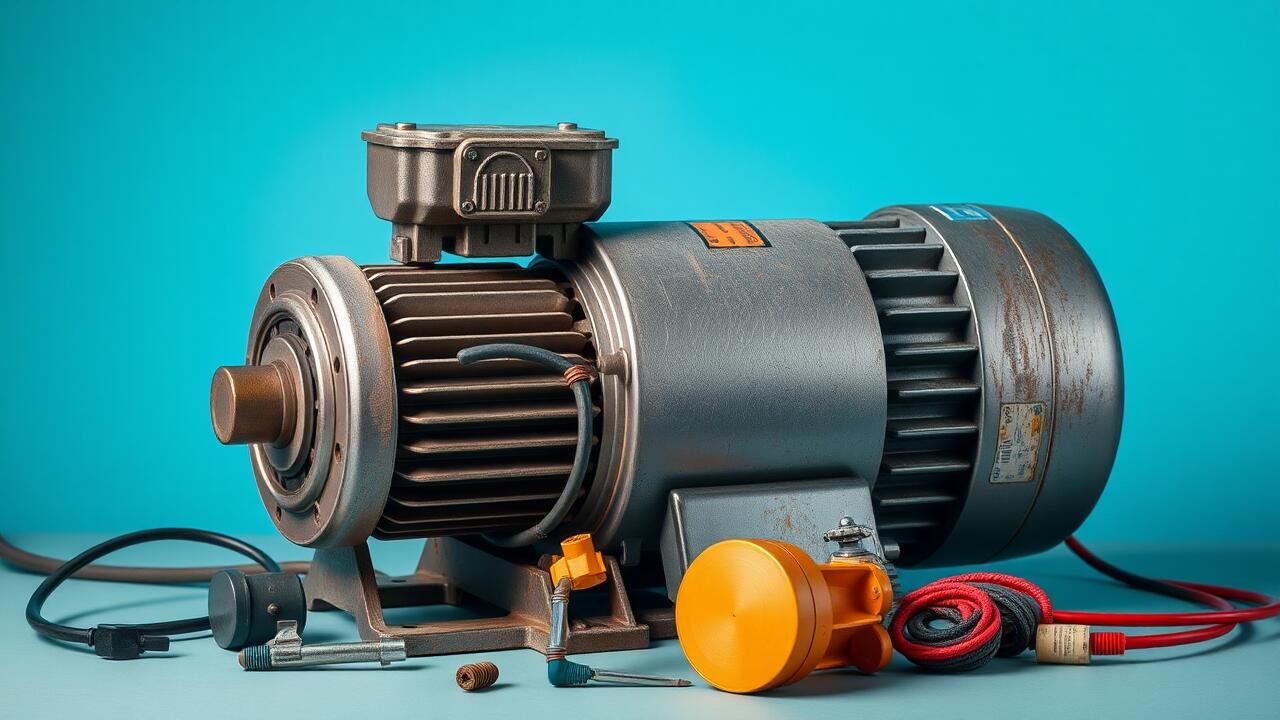
Importance of Timely Motor Repair
Timely industrial motor repair is crucial for maintaining the operational efficiency of machines in various industries. Neglecting the repair of components like DC motors and induction motors can lead to untimely breakdowns, affecting production lines. Regular inspections and routine maintenance not only prevent costly repairs but also ensure that machines, such as industrial shredders, operate at their best. A proactive approach helps in identifying potential issues before they escalate into major failures.
Delaying motor repairs can significantly impact productivity and safety within a machine shop. A malfunctioning motor can cause machinery to perform poorly or even halt operations altogether. This disruption affects not just the equipment itself but also the entire workflow, leading to delays and increased labor costs. By prioritizing industrial motor repair and maintenance, businesses can ensure their machines are reliable and effective, ultimately enhancing performance and extending the lifespan of their equipment.
Common Issues with Industrial Motors
Industrial motors often face a variety of challenges that can disrupt manufacturing processes. Overheating is a prevalent issue, often resulting from inadequate maintenance or wear and tear over time. Regular checks and timely industrial motor repair can help identify potential problems before they escalate. Synchronous motors, in particular, may experience issues with field excitation, leading to diminished performance. Engineers must be adept at understanding the specific requirements of different manufacturers to effectively address these issues.
Electrical failures are another common concern that significantly impacts the efficiency of industrial motors. Issues like insulation breakdown or short circuits can arise due to improper installation or external damages. Knowledge of how to reverse engineer these electrical failures is crucial for effective industrial motor repair. Manufacturers benefit from having a well-defined maintenance schedule in place to mitigate the risks associated with such issues, ensuring that their motors operate at optimal capacity.
Types of Electric Motor Repair
Understanding the different approaches to electric motor repair is essential for maintaining the efficiency of an electrical power system. Industrial motor repair encompasses various techniques tailored for AC and DC motors, considering their unique characteristics and requirements. Repairing gearboxes and electronics associated with motors often requires specialized knowledge, particularly in handling transformers and other components integral to the electrical power network. Qualified technicians perform preventive maintenance to anticipate potential issues, ensuring the reliable operation of industrial motors. By employing appropriate repair methods, businesses can extend the lifespan of their equipment while minimizing downtime and operational costs.
AC vs. DC Motor Repair Techniques
Repair techniques for AC and DC motors exhibit distinct methodologies rooted in their operational principles. AC motors, commonly used in pumps and other industrial applications, often require attention to their winding configurations and stator components. Troubleshooting techniques involve examining the electrical supply, looking for misalignments, or assessing the condition of the bearings. Such assessments are crucial in ensuring efficient electric motor repair, particularly for machines operating under heavy loads.
DC motors, on the other hand, focus on components like commutators and brushes, integral to their functionality. Engineering strategies for industrial motor repair in DC motors may involve cleaning or replacing these parts to restore performance. Understanding the unique technologies and issues associated with each type of motor is vital for effective motor repair. Proper diagnosis can significantly enhance operational efficiency and prolong the lifespan of both AC and DC systems in industrial settings.
Specialized Repair for Different Motor Designs
Different types of industrial motors require specific approaches to repair based on design and functionality. Electric motor repairs can vary widely, taking into account factors such as winding configurations, rotor types, and application requirements. A specialized motor repair service is essential for addressing unique challenges that arise in these various designs. The industrial motor division often focuses on tailored industrial motor solutions to ensure optimal performance and longevity, recognizing that a one-size-fits-all approach may not suffice.
Understanding the particularities of each motor design plays a critical role in the success of industrial motor repair. Skilled technicians are trained in various industrial motor service techniques, allowing them to execute repairs that restore efficiency and reliability. Whether dealing with an AC or DC motor, expertise in these specialized repair processes enhances the overall quality of industrial repair work. Routine assessments and proactive maintenance can further contribute to reducing downtime and ensuring that each motor operates efficiently.
Identifying Industrial Motor Needs
Assessing performance and efficiency plays a crucial role in determining the need for industrial motor repair. Regular evaluations help identify issues in various types of industrial motors, such as those used in industrial shredder motors. Electric motor manufacturers emphasize the importance of monitoring operational metrics to ensure efficiency. Electric motor experts recommend routine inspections, which can be conducted at specialized motor shop facilities, to spot early signs of deterioration. By understanding the available motor solutions, businesses can make informed decisions about whether to repair or replace their motors, ultimately ensuring longevity and optimal performance in their operations.
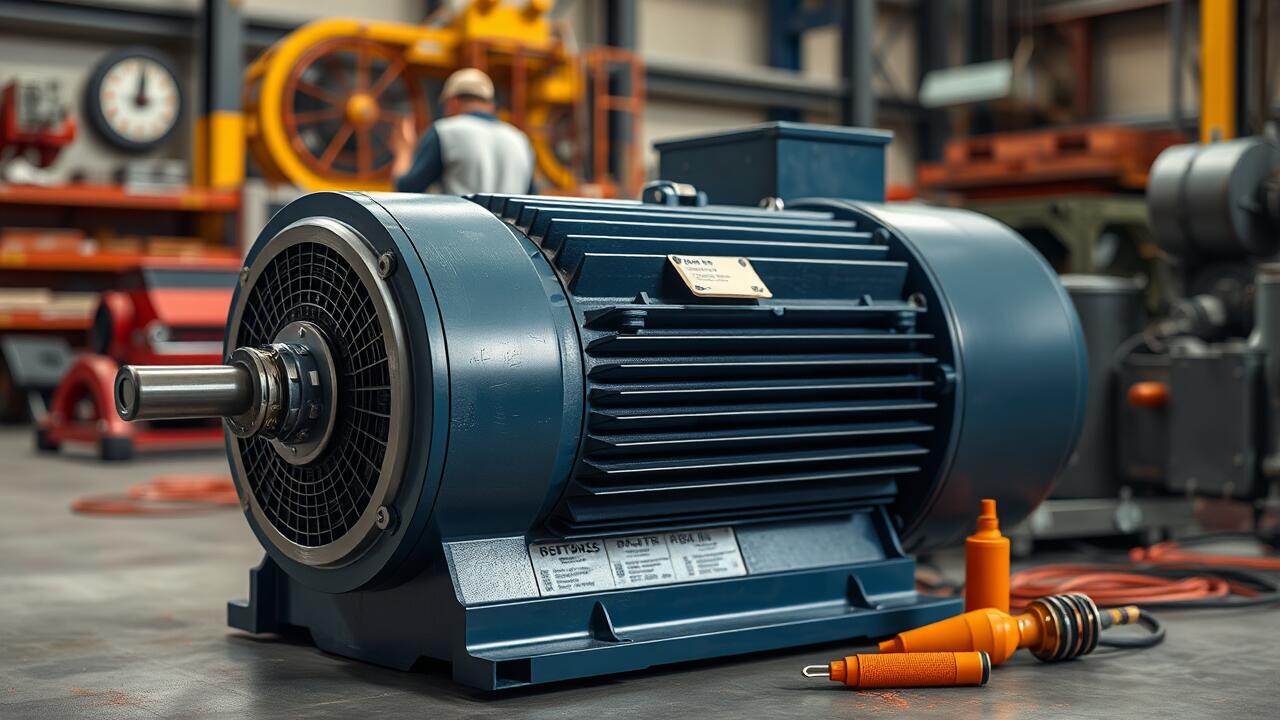
Assessing Performance and Efficiency
Evaluating the performance and efficiency of an in-use motor is crucial for effective industrial motor repair. Analyzing parameters such as operating temperature, noise levels, and vibration can provide insight into potential issues. If the original motor is showing signs of wear or inefficiency, it may require electric motor rewinding or other specialized repairs. Consultation with a reputable repair shop can help determine the best approach tailored to the specific motor application.
Key performance indicators often signal whether a motor requires attention. A noticeable drop in efficiency or increased operational costs may point to underlying problems necessitating professional service. A reliable generator repair company can assess the condition of the motor and recommend appropriate solutions. Regular performance assessments ensure that the industrial motor repair process is proactive rather than reactive, ultimately enhancing productivity and longevity.
Signs Indicating Repair or Replacement
Unusual noises, vibrations, or inefficient performance are strong indicators that an industrial motor requires attention. Such signs may suggest wear and tear or deeper issues that could lead to failures. Prompt industrial motor repair becomes critical to prevent operational downtime. An authorized repair facility often provides the same repair capabilities as the original manufacturer, ensuring that repairs are conducted with expertise. Ignoring these signs may escalate the need for extensive pump repair or other motor services.
Another indication that repair or replacement is needed is increased energy consumption which can signal inefficiencies in motor function. This inefficiency is particularly concerning for custom motors designed for specific applications. Regular assessments by professionals in industrial motor repair can help determine whether repairing existing equipment or investing in new motors is more cost-effective. Many motor services offer detailed diagnostics to support informed decisions regarding the best course of action.
The Repair Process for Industrial Motors
A comprehensive understanding of the repair process is essential for effective industrial motor repair. This process typically begins with diagnosing issues related to both AC and DC motors. Skilled technicians assess the condition of industrial controls and identify any malfunctioning components. Following diagnosis, repair services engage in detailed maintenance jobs, which may include rewinding, replacing parts, or calibrating the motors. Keeping spare motors readily available can expedite the repair process, minimizing downtime. Each step in the procedure is crucial for ensuring that service motors operate efficiently and reliably after repairs are completed.
Step-by-Step Repair Procedure
A systematic approach is vital for effective industrial motor repair. Technicians with experience repairing various types of motors, including horizontal shaft motors and u-frame motors, can efficiently diagnose issues that may arise. The initial step typically involves thorough inspection to identify faults in electrical equipment and mechanical components. For instance, a common challenge in shredder motors may include overheating or unusual noises, necessitating an in-depth analysis to pinpoint underlying problems.
Following the inspection, the repair process focuses on disassembly of the motor for further examination. Components such as bearings, windings, and insulation need careful evaluation and possible replacement. Skilled professionals in the industrial industry utilize specialized tools and techniques tailored to each motor type. Ensuring that all parts are properly cleaned and lubricated is essential before reassembly. This detailed approach guarantees the motor operates at peak performance upon completion of the industrial motor repair.
Tools and Equipment Used in Motor Repair
The successful execution of industrial motor repair relies heavily on specialized tools and equipment. Technicians often use diagnostic tools to identify issues in wound motors, ensuring that repairs are precise and effective. On-location repair services commonly require mobile equipment that can handle various motor types, including those manufactured by prominent drive system manufacturers like Baldor and Reliance. Utilizing such equipment not only reduces downtime but also helps manage the electrical equipment cost associated with repairs.
A thorough understanding of the required tools enhances the efficiency of repair processes. For instance, proper lifting gear is essential for handling heavy industrial motors, while testing devices are crucial for assessing performance post-repair. Repair professionals also frequently work with used equipment to offer cost-effective solutions. By employing the right tools, repair services can extend the lifespan of industrial motors and improve overall operational reliability.
- Proper diagnostic tools for identifying motor issues
- Mobile equipment for on-location repairs
- Lifting gear for handling heavy motors
- Testing devices for post-repair performance assessment
- Used equipment for cost-effective repair solutions
- Maintenance tools for routine inspections
- Safety equipment to ensure technician protection during repairs
Best Practices for Spare Motor Maintenance
Routine maintenance is essential for ensuring the longevity and reliability of in-stock motors. Regular checks can prevent the need for extensive industrial motor repair by identifying minor issues before they escalate. Proper storage conditions play a vital role in maintaining equipment; exposure to dust, moisture, and extreme temperatures can negatively affect motors. Leveraging manufacturing expertise can streamline the maintenance process, ensuring that each motor meets electrical apparatus needs efficiently. Collaborating with companies like ISS Motor Control can enhance total equipment management strategies, including new equipment sales and the provision of tailored maintenance programs. Keeping spare motors ready for use requires a strategic approach to routinely evaluate their performance and condition, thereby minimizing downtime and optimizing operational efficiency.
- Ensure motors are stored in a clean, dry environment to prevent corrosion and damage.
- Conduct regular visual inspections to check for signs of wear or leakage.
- Rotate and exercise spare motors periodically to keep components moving and maintain functionality.
- Maintain proper documentation of maintenance activities and inspection reports for each motor.
- Schedule routine tests such as insulation resistance and winding resistance checks.
- Develop a maintenance log that includes the date of maintenance, checks performed, and any findings.
- Train staff on best practices for handling and maintaining spare motors to reduce mishandling risks.
Routine Maintenance Tips
Regular inspections of industrial motors are crucial for identifying potential issues before they escalate. Industrial users should implement routine maintenance programs that include visual checks for signs of wear, unusual noises, or overheating. Engaging with a professional rebuilder or electrical apparatus service can provide manufacturers with the expertise necessary to maintain optimal performance. A full machine shop equipped for industrial motor repair allows for immediate attention to any findings during inspections.
Maintenance should also include keeping detailed records of performance metrics and repair history. This documentation aids in recognizing patterns that may indicate deeper-rooted problems. Custom manufacture components can enhance the longevity of the equipment, ensuring that any replacements are specifically tailored to the original specifications. By prioritizing these routine maintenance tips, industrial users can minimize downtime and extend the life of their motors.
Keeping Spare Motors Ready for Use
Having spare motors readily available can significantly minimize downtime during unexpected failures. Several industries rely on industrial motor repair to ensure smooth operations. Major manufacturers produce robust motors, but even the best equipment can experience issues. Engineers emphasize the importance of not only having spare motors on hand but also ensuring they are well-maintained. Skilled craftsmen can assist contractors in preparing these spares, helping to streamline the repair process when needed.
Regular checks and maintenance of spare motors are crucial for optimal performance. Contractors and manufacturers must collaborate to identify potential issues before they arise. This proactive approach ensures that spare motors are in working condition and ready for immediate deployment. By investing in proper storage and upkeep, organizations can guarantee that their spare motors remain effective resources during critical repair times.
Selecting a Professional Repair Service
Choosing the right professional service for industrial motor repair is crucial for maintaining the efficiency of turbine equipment across various industries. Rebuilt motors can significantly enhance operational reliability and longevity, so partnering with skilled craftsmen who specialize in this field is essential. Engaging onsite maintenance partnerships can streamline the repair process and minimize downtime. Utilizing auxiliary contractors who possess expert knowledge of industrial motor repair ensures that the work is completed to the highest standard, providing reliable solutions tailored to your specific needs. Prioritizing these factors will lead to effective maintenance and improved performance of your industrial equipment.
Conclusion
Understanding the intricacies of industrial motor repair is essential for maintaining optimal operational efficiency within any industry. Partnering with an SKF-certified rebuilder ensures that your motors receive quality workmanship tailored to their specific needs. This expertise not only addresses common issues such as shaft misalignment or bearing failures but also supports retrofit projects aimed at enhancing performance. Prioritizing industrial motor repair can significantly extend the lifespan of your equipment and optimize its performance, maintaining smooth operations and reducing downtime. Recognizing the importance of quality workmanship in every step of the repair process leads to better outcomes and sustained productivity.
FAQS
What is industrial motor repair?
Industrial motor repair refers to the process of diagnosing, troubleshooting, and fixing problems in electric motors used in various industrial applications to ensure they operate efficiently and reliably.
Why is timely motor repair important?
Timely motor repair is crucial because it helps prevent more significant issues, reduces downtime, improves operational efficiency, and extends the lifespan of the motor, ultimately saving costs in the long run.
What are common issues that can occur with industrial motors?
Common issues with industrial motors include overheating, unusual vibrations, electrical failures, bearing wear, and misalignment, which can lead to decreased performance and potential motor failure.
What are the different types of electric motor repair?
The different types of electric motor repair include mechanical repairs (like bearing replacements), electrical repairs (such as rewinding coils), and comprehensive overhauls that may involve replacing various internal components.
How do AC and DC motor repair techniques differ?
AC motor repair often focuses on issues related to stator and rotor windings and may require different tools for analyzing alternating current. In contrast, DC motor repair may involve brush replacement and commutator servicing, necessitating different techniques and tools.
What specialized repairs exist for different motor designs?
Specialized repairs may involve tailored techniques for specific motor designs, such as stepper motors, servo motors, and synchronous motors, which have unique components and operational characteristics requiring specialized knowledge.
How can I identify my industrial motor needs?
Identifying motor needs involves assessing the application's requirements, including load specifications, efficiency expectations, and environmental conditions, as well as reviewing the motor's current performance and maintenance history.
What signs indicate that an industrial motor needs repair or replacement?
Signs that indicate a motor needs attention include abnormal noises, excessive heat, decreased efficiency, frequent tripping of overloads, and visible wear or damage to components.
What is the typical repair process for industrial motors?
The typical repair process includes diagnosing the problem, disassembling the motor, inspecting components, performing necessary repairs or replacements, reassembling the motor, and conducting final testing to ensure it operates correctly.
What tools and equipment are used in motor repair?
Common tools and equipment used in motor repair include multimeters, oscilloscopes, vibration analysis tools, torque wrenches, and specialized motor service tools such as bearing pullers and winding machines.
What are the best practices for spare motor maintenance?
Best practices for spare motor maintenance include regular inspections, proper storage conditions, periodic testing, and ensuring that motors are adequately lubricated to prevent deterioration while not in use.
How can I keep spare motors ready for use?
Keeping spare motors ready for use involves maintaining them in a clean and dry environment, regularly checking for signs of wear or damage, and performing routine maintenance to ensure they are operational when needed.
How do I select a professional repair service for industrial motors?
To select a professional repair service, consider factors such as their experience in the industry, certifications, customer reviews, response time, and whether they provide a warranty for their work to ensure quality service.
How do advancements in technology affect the repair of AC/DC motors in an electric motor shop?
Advancements in technology have significantly improved the efficiency and effectiveness of repair services for AC/DC motors in electric motor shops. For example, modern electric motor shops now utilize advanced diagnostic tools that enhance the reliability of solutions offered. Additionally, companies often incorporate new equipment sales to ensure that they are using the best tools available for motor repair, particularly for brands like Baldor and Reliance. This focus on technology helps ensure that repairs are not only effective but also aligned with the latest standards in motor repair and maintenance.
What are some reliability solutions available for Baldwin/Reliance motors during the repair process in industrial settings?
In industrial motor repair, reliability solutions for Baldor/Reliance motors often include the use of advanced diagnostic equipment, which can aid in identifying issues before they lead to failures. Additionally, new equipment salesstay focused on improving motor efficiency and longevity, ensuring that repairs can be completed swiftly while maintaining high standards of performance.
What are the best practices for maintaining Baldor/Reliance motors to minimize the need for industrial motor repair?
To minimize the need for industrial motor repair, it's essential to follow best practices for Baldor/Reliance motors, which include regular inspections, proper lubrication, ensuring clean ventilation, and monitoring for unusual vibrations or noises. Implementing a preventive maintenance schedule can significantly extend the lifespan of your motors and reduce the need for unplanned repairs in industrial settings.
What specific challenges do technicians face when repairing Baldor/Reliance motors, and how can they effectively overcome them?
Technicians often encounter issues such as difficulty sourcing parts, understanding the specific design features of Baldor/Reliance motors, and ensuring proper calibration during repair. To effectively overcome these challenges, it's important to have thorough training on the intricacies of these motors, develop relationships with reliable suppliers for parts, and utilize diagnostic tools designed for Baldor/Reliance motors to ensure precise repairs and optimal performance.
What types of repairs are commonly performed on Baldor/Reliance motors in an industrial setting?
Common repairs performed on Baldor/Reliance motors in an industrial setting include rewinding the motor coils, replacing bearings, and addressing insulation failures. These tasks are essential to ensure the longevity and efficiency of motors, especially given their critical role in various industrial applications.
What are the key indicators that might suggest the need for repair on Baldor/Reliance motors in an industrial environment?
Key indicators for repair on Baldor/Reliance motors include unusual noises, excessive vibration, overheating, and decreased performance. Regular monitoring of these symptoms in motors can help prevent more extensive issues that require industrial motor repair.
What are the most common types of motors used in industrial applications, specifically regarding Baldor/Reliance motors?
In industrial applications, the most common types of motors include AC motors and DC motors, with Baldor/Reliance motors being particularly popular due to their reliability and performance. Repair services often focus on maintaining these motors, ensuring they operate efficiently, and addressing any issues that may arise in the industrial environment.
What essential maintenance tips can be implemented to extend the lifespan of Baldor/Reliance motors in industrial applications?
To extend the lifespan of Baldor/Reliance motors in industrial applications, it is important to implement regular maintenance practices such as routine inspections, lubrication of moving parts, and monitoring for any unusual sounds or vibrations. Additionally, ensuring that the motors are kept free of dust and debris, and that electrical connections are secure, will help maintain efficiency and reduce the likelihood of breakdowns. Regular maintenance can significantly mitigate the need for complex repairs on these motors.
What preventive measures can industrial facilities take to reduce repair needs for Baldor/Reliance motors?
Implementing regular maintenance schedules, conducting thorough inspections, and using quality replacement parts are essential preventive measures that help extend the life of Baldor/Reliance motors and reduce the likelihood of needing repairs. This proactive approach ensures that motors remain operational and less prone to breakdowns.
What factors contribute to the increased demand for industrial motor repair services for Baldor/Reliance motors?
The increased demand for industrial motor repair services for Baldor/Reliance motors can be attributed to several factors, including the aging of existing motors, the high operational intensity in industrial settings, and the need for specialized knowledge to address specific issues that arise in Baldor/Reliance motors. Additionally, maintenance practices directly impact the frequency of repairs, as improper use can lead to more significant problems, thus necessitating professional repair services.