Exploring the Benefits of Thermistors for Electric Motors
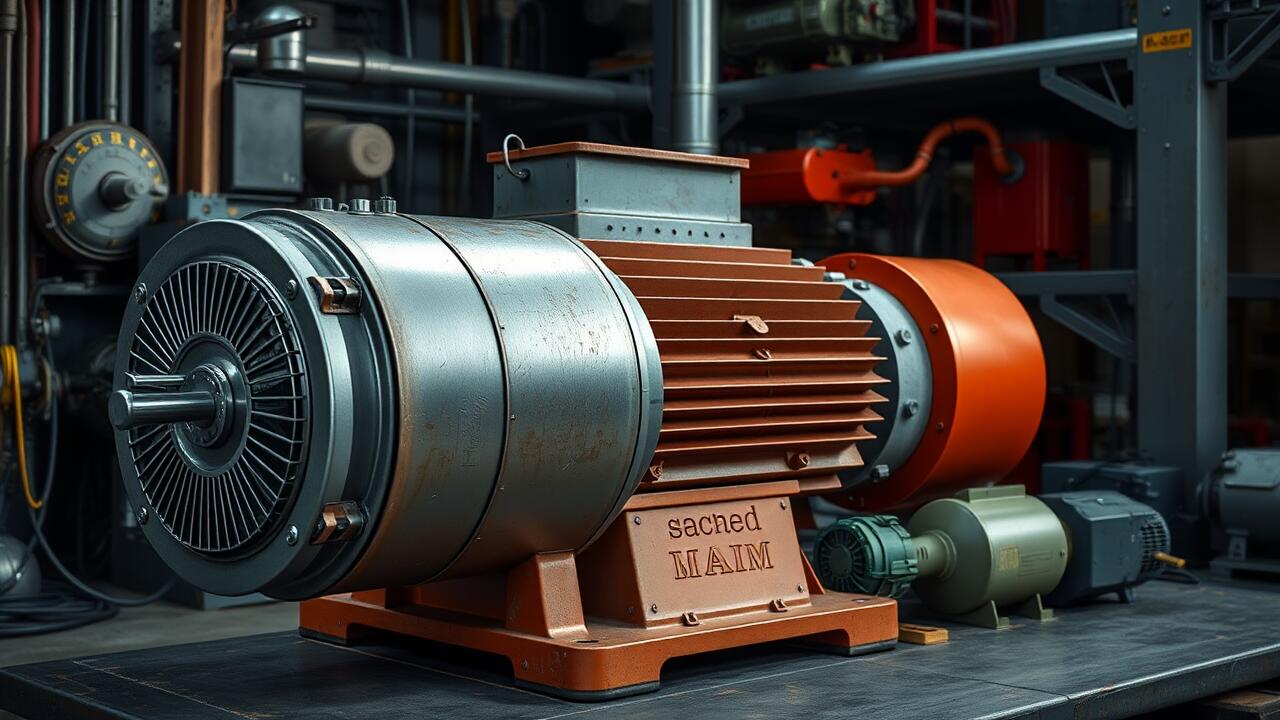
Table Of Contents
Key Takeaways
- Comprehending Thermistors and Their Functionality
- The Importance of Thermistors in Motor Operations
- Advantages and Uses of Thermistors in Electric Motors
- Thermistors for Current Safeguarding
- Choosing the Appropriate Thermistor for Motors
- Setup and Care for Thermistors in Electric Motors
Understanding Thermistors
Thermistors are crucial components widely used in electric motors to monitor and regulate temperature. These temperature-sensitive resistors come in two main types: negative temperature coefficient (NTC) thermistors and positive temperature coefficient (PTC) thermistors. NTC thermistors decrease in resistance as temperature rises, making them ideal for precise temperature measurements, while PTC thermistors increase resistance with temperature, providing effective overcurrent protection. The integration of thermistors for electric motors enhances efficiency and performance by ensuring optimal operating conditions, safeguarding against overheating, and extending the lifespan of electrical motors. Proper understanding of thermistors, including their specific functionalities and applications, is essential for selecting the right components in motor design and operation.
Definition and Functionality
Thermistors for electric motors are temperature-sensitive resistors that play a crucial role in various types of electrical machines, including induction motors and AC motors. These devices are designed to change their resistance in response to temperature fluctuations, allowing them to effectively monitor and regulate the temperature of the electric motor. This functionality is essential for preventing overheating and ensuring optimal performance, particularly in motors that rely on coils for their operation.
These thermistors operate by integrating within the circuit diagrams of electric motors, strategically placed near vital components such as power semiconductor devices. Their electrically insulating properties help maintain the integrity of the motor's performance while providing accurate temperature measurements. By responding dynamically to changes, thermistors for electric motors enhance both efficiency and reliability, ultimately contributing to the longevity of the electrical systems they are part of.
Types of Thermistors
Thermistors for electric motors are primarily categorized into two types: NTC (Negative Temperature Coefficient) and PTC (Positive Temperature Coefficient) thermistors. NTC thermistors exhibit a decrease in electrical resistance as the temperature increases, making them ideal for temperature sensing and compensation in circuits. PTC thermistors, on the other hand, increase their resistance with rising temperatures, which can be beneficial for overcurrent protection in various electrical elements, including machines and transformers. Both types play a crucial role in managing voltage and current flow.
The application of thermistors in electric motors extends beyond simple temperature monitoring. In circuits where electrical resistance is critical, thermistors can help regulate electricity, enhancing the overall safety and efficiency of motor operation. High voltage scenarios benefit from the incorporation of thermistors that can manage power transistor functionality, ensuring stable performance. This versatility makes thermistors for electric motors indispensable components in designing reliable and efficient electrical systems.
The Role of Thermistors in Electric Motors
Thermistors for electric motors play a crucial role in optimizing performance and ensuring reliable operation. These semiconductor devices serve as temperature sensors, effectively monitoring the thermal conditions within the motor components, such as the rotor and circuitry. Their ability to provide precise readings allows for effective management of self-regulating heating elements, ensuring that the motor operates within safe temperature limits. In applications like compressors and industrial electronics, thermistors enable better integration with motor control systems, safeguarding copper conductors and litz wires from overheating. By maintaining the right thermal environment, thermistors contribute significantly to the efficiency and longevity of electric motors.
Importance of Temperature Sensing
Temperature sensing is critical in maintaining the performance of electric motors. Thermistors for electric motors act as reliable sensors that monitor the temperature of motor windings. These components alter their resistance based on temperature changes, allowing for real-time data collection. This data is essential for preventing overheating, which could lead to motor failure. Integrating a thermistor into the motor's circuitry can create a feedback mechanism that optimizes the operation, enhancing efficiency and longevity.
A resistance thermometer, such as a thermistor, provides a precise reading of temperature fluctuations. The relationship between resistance and temperature enables accurate monitoring of the motor's operating conditions. This ensures that electronics like transistors and other components function within safe temperature limits. Properly placed temperature sensors, along with a well-designed diagram of the motor's internal structure, can help engineers better understand and manage thermal dynamics. Thus, employing thermistors for electric motors is vital for effective temperature regulation.
- Ensures the prevention of costly motor failures due to overheating.
- Enhances overall operational efficiency of electric motors.
- Contributes to the longevity of both motor and electronic components.
- Allows for accurate monitoring and quick response to temperature changes.
- Supports the design of better thermal management systems in engineering applications.
- Helps in optimizing performance under varying load conditions.
- Facilitates compliance with safety standards and regulations in motor operation.
Integration with Motor Control Systems
Thermistors for electric motors play a crucial role in the integration with motor control systems. These components act as essential thermistor sensors, providing real-time temperature data to assist control algorithms. The specific thermistor selected can significantly influence how the motor operates under varying conditions. By using power thermistor components, systems can enhance their response to temperature changes, ensuring optimal performance across different loads. Such integration improves overall system reliability and efficiency, making it vital for advanced motor applications.
Effective motor protection thermistors safeguard electric motors against overheating, ensuring they remain within safe operating limits. These thermistors motor sensor technologies continually monitor the temperature and relay critical data to the control system. A PTC thermistor motor, for example, can help to automatically limit current flow when temperatures exceed predefined thresholds. This proactive approach to thermal management not only enhances motor longevity but also ensures that the system remains responsive to abnormalities, reinforcing the importance of integrating thermistors in modern motor control frameworks.
Thermistors for Electric Motors: Benefits and Applications
Thermistors for electric motors play a crucial role in enhancing efficiency and performance across various applications. Utilizing single thermistors, such as a PTC thermistor, offers a cost-effective solution for temperature sensing and protection. The thermistor type chosen impacts the thermistor elements’ ability to manage fluctuations in motor operation. Single thermistor installations benefit from high thermistor input resistance, ensuring reliable circuit functionality. Inexpensive thermistors can significantly reduce overall system costs while maintaining optimal thermistor resistance. By incorporating protection thermistors, electric motors can operate safely under varying conditions, ultimately improving reliability and extending the lifespan of the motor components.
Enhancing Efficiency and Performance
Thermistors for electric motors play a crucial role in enhancing overall efficiency and performance. The use of NTC thermistors allows for precise temperature measurements that help regulate motor operation, preventing overheating and ensuring optimal functioning. PTC thermistors products, known for their ability to react to temperature changes rapidly, contribute significantly to protective measures within electric motors. Companies like Siemens integrate advanced thermistors into their designs, ensuring stability and reliability in performance while reducing energy consumption.
The unique characteristics of PTC thermistors, such as their self-resetting capabilities, make them ideal for current protection in various applications. The manufacturing of PTC thermistor sensors focuses on achieving high sensitivity and durability, which is essential for maintaining efficiency across different motor types. Amwei PTC thermistors exemplify quality in this field, providing effective solutions for motor applications that require robust thermal management. The integration of triple thermistor setups can optimize the monitoring of multiple temperature zones, further improving electric motor performance.
Use Cases in Various Motor Types
Thermistors for electric motors play a crucial role across various applications, particularly in ensuring the safety and efficiency of electrical motors. Negative temperature thermistors are frequently employed in the design of motor circuits due to their ability to respond rapidly to temperature changes. These sensor PTC thermistors help maintain optimal operating conditions by limiting the maximum temperature reached by the motor. Their specific thermistor trip temperature allows for proactive management of thermal events, preventing potential damage and extending the life of the motor.
Different types of electric motors utilize PTC thermistors for different purposes. Purpose PTC thermistors are often integrated into applications ranging from household appliances to industrial machinery. Reliable PTC thermistors offer consistent performance, with a PTC thermistor limit that protects against overcurrent conditions. The resistance characteristics of PTC thermistor resistance enable users to achieve precise temperature control, thereby ensuring stable operation in diverse motor types, including brushless DC motors and stepper motors.
Current Protection Thermistors
Protecting electric machines from overcurrent conditions is essential for maintaining their longevity and efficiency. PTC thermistors play a crucial role in this protection by offering a simple but effective mechanism that responds to changes in temperature. The PTC thermistor temperature rises as current increases, causing the thermistor to shift to a high-resistance state, thereby limiting the current flow. Various types of PTC thermistors, such as mod-tronic PTC thermistors and ceramic PTC thermistors, are commonly used in open motors and three-phase motors. Understanding the characteristics of different thermistors for electric motors requires consulting a thermistor selection chart, which can guide users in choosing the right components, including PTC thermistor beads. The NTC thermistor beta value is also important for applications where precise temperature sensing is paramount. Proper integration of these components enhances the overall performance of electric machines while ensuring their protection from damaging overcurrents.
Mechanism of Current Protection
Thermistors for electric motors play a crucial role in current protection by monitoring temperature changes within motors. As electric currents flow through three-phase induction motors and single-phase induction motors, excessive heat can develop due to overload conditions. Thermistors, by sensing this rise in temperature, can trigger protective mechanisms that limit base-emitter voltage, ensuring that the motors operate safely. This proactive approach helps to prevent damage and extends the lifespan of motors, including small motors and TEFC motors.
The incorporation of thermistors for electric motors enhances the reliability of motor operation. By effectively regulating base voltage, these devices can prevent overheating and reduce the risk of failures in various applications. With the increasing demand for efficiency in electric today, a motors® brand product featuring thermistors offers a sophisticated solution for safeguarding motor performance. Implementing current protection mechanisms is essential for maintaining optimal functionality and protecting the investment in electric motor technology.
Advantages in Motor Operation
Thermistors for electric motors play a crucial role in monitoring the motor windings temperature, ensuring optimal performance. They act as key motor sensor features, providing real-time data that protects the whole circuit from potential overheating. By accurately gauging the temperature of the electrical windings, thermistors help prevent damage to components, enhancing the reliability of different circuits within the system.
These temperature sensors also contribute significantly to the safe operation of ATEX motors by ensuring that the auxiliary coil functions effectively under varying operating voltage conditions. By maintaining the proper thermal balance, thermistors for electric motors not only safeguard the integrity of the motor winding but also promote energy efficiency, which can lead to extended lifespan and reduced maintenance needs.
Selecting the Right Thermistor for Electric Motors
Choosing the appropriate thermistors for electric motors is vital for ensuring optimal performance and reliability in various machines. These components function effectively in such circuits by monitoring motor temperature and providing circuit protection. Key specifications to consider include the thermistor's response time and resistance characteristics, particularly for applications requiring a non-adjustable switch point. Integrating thermistors into transistor circuits enhances the efficiency of non-rotor systems and protects motor windings from overheating. A thorough understanding of these elements is essential for determining compatibility with motor designs and ensuring reliable electrical protection throughout operation.
Key Specifications to Consider
Selecting the right thermistors for electric motors involves understanding specific specifications that impact performance. Key factors include resistance test voltage, ensuring the thermistor can operate effectively within the motor's expected voltage levels. Thermistors must also be compatible with control systems temperature requirements and able to endure the conditions set by the motor's simple starter circuit. For applications like locked rotor protection, proper calibration is essential to guarantee reliable function in shutdown circuits that prevent damage from overheating.
Attention must also be paid to the characteristics of motor protection sensors and their integration with comparator circuits. These circuits play a crucial role in assessing the thermal conditions and switching accordingly. Calco electric provides insight into selecting thermistors that suit various motor designs, focusing on performance metrics such as response time and stability under variable operating conditions. Understanding these specifications ensures that the selected thermistors can effectively contribute to enhanced motor safety and efficiency.
Compatibility with Motor Designs
Selecting the appropriate thermistors for electric motors involves understanding the specific requirements of the motor design. This includes evaluating parameters such as maximum voltage and test voltage. Thermistors must integrate seamlessly with motor protection modules and existing equipment to ensure reliable operation. In many cases, they work alongside bimetallic switches and automatic circuit breakers to enhance thermal management capabilities, contributing to the overall safety of the motor.
Compatibility also hinges on the effective functioning of temperature sensors within the control module. Ensuring that thermistors for electric motors can accurately monitor temperature changes is crucial for maintaining optimal performance. The right thermistor type can bolster motor efficiency and prevent overheating, which is essential for long-term operation in various applications. Proper selection and installation significantly affect how well the motor adapts to its environment, thereby impacting its overall lifespan.
Installation and Maintenance of Thermistors
Correct installation and routine maintenance of thermistors for electric motors are essential for optimal performance and longevity. Properly integrating these temperature sensing devices into the controller ensures that the windings are protected from overheating. Models like the amwei NTC C512 and C513 play pivotal roles in monitoring the operating conditions, providing critical feedback to the motor control system. Regular checks on the functionality of limit temperature sensors, such as the C509, can prevent damage by enabling timely responses to deviations in power or temperature. Comprehensive understanding of these components enhances reliability in motor operation and boosts overall efficiency.
- Ensure proper orientation when installing thermistors to avoid incorrect readings.
- Regularly inspect connections for corrosion or wear to maintain electrical integrity.
- Test thermistor functionality with a multimeter to confirm accurate temperature readings.
- Keep thermistors clean from contaminants that could affect performance.
- Follow manufacturer guidelines for installation depth and environment to ensure longevity.
- Schedule periodic maintenance checks to identify potential issues before they escalate.
- Document all maintenance activities to track performance and adjustments over time.
Conclusion
Thermistors for electric motors play a crucial role in enhancing the efficiency and performance of both single-phase induction motors and three-phase induction motors. By effectively managing base-emitter voltage, these devices ensure that electric motors operate within safe temperature ranges, preventing overheating and potential damage. The use of thermistors is particularly beneficial in TEFC motors and small motors, where precise temperature control is vital. Many manufacturers now offer thermistors as part of their motors® brand product line, catering to the diverse needs of the industry. Understanding the functionality and specifications of thermistors for electric motors is essential for optimizing performance in electric applications today.
FAQS
What is a thermistor and how does it work in electric motors?
A thermistor is a type of temperature sensor made from ceramic materials that exhibit a change in resistance with temperature variations. In electric motors, thermistors monitor the motor's temperature to prevent overheating and ensure optimal performance.
What are the different types of thermistors used in electric motors?
The two main types of thermistors are Negative Temperature Coefficient (NTC) and Positive Temperature Coefficient (PTC) thermistors. NTC thermistors decrease in resistance with increasing temperature, while PTC thermistors increase in resistance with rising temperature.
Why are thermistors important for temperature sensing in electric motors?
Thermistors provide accurate and timely temperature measurements, allowing for effective monitoring of motor conditions. This helps in protecting the motor from thermal damage and improving overall efficiency and performance.
How do thermistors integrate with motor control systems?
Thermistors are integrated into motor control systems to provide real-time temperature data, enabling automatic adjustments to power input or cooling mechanisms. This integration helps maintain optimal operating conditions and prolongs motor lifespan.
What are the key specifications to consider when selecting a thermistor for electric motors?
Important specifications include temperature range, resistance value, response time, and compatibility with the motor design. It's essential to choose a thermistor that meets the specific requirements of the electric motor application.
What are the key characteristics of PTC thermistors used in electric motors for temperature protection applications?
PTC thermistors are crucial for temperature protection in electric motors. They are part of PTC thermistors sensors, which serve to safeguard the motor against overheating. The PTC thermistor characteristics include their ability to change resistance significantly at a specific temperature, enabling them to function effectively in PTC type thermistors circuits. Siemens thermistors often utilize this technology in their designs. Moreover, the manufacturing processes for NTC thermistor manufacturing and PTC thermistors manufacturing ensure high reliability. The PTC thermistor returns to a low-resistance state once the temperature drops, making them efficient unit switches in electric motor applications.
How can PTC thermistors provide temperature protection in electric motors used in vacuum applications?
PTCs thermistors are ideal for temperature protection thermistors in electric motors, especially in vacuum environments. These thermistors operate within a PTC thermistors circuit, which ensures that when the temperature rises, the resistance increases sharply, thereby limiting current flow and preventing damage to the motor from overheating. This mechanism is essential for safeguarding electric motors in temperature-sensitive applications.
What role do thermistors play in enhancing the efficiency of electric motors?
Thermistors are crucial in electric motors as they help regulate temperature, which enhances the efficiency of the motor. By monitoring temperature changes, a thermistor can signal when to adjust the electrical flow, preventing overheating and thereby maintaining optimal performance levels.
How do thermistors contribute to the overall safety of electric motors?
Thermistors are crucial for the safety of electric motors as they monitor temperature and can prevent overheating by triggering protective measures when a certain temperature threshold is reached.
How do thermistors interact with electric motor control systems to optimize performance?
Thermistors are critical components in electric motor control systems, as they help monitor temperature and provide feedback for optimal performance. By accurately sensing changes in temperature, a thermistor can inform the control system to adjust operation parameters, preventing overheating and ensuring efficient motor function. This feedback loop enhances reliability and longevity, making the thermistor an essential part of electric motor design.
What are the advantages of using thermistor technology in electric motor applications?
The advantages of using thermistor technology in electric motor applications include improved temperature monitoring, enhanced safety features, and the ability to provide accurate thermal feedback. Thermistors can detect temperature rises quickly, preventing overheating and potential motor failure, thus ensuring the longevity and efficient performance of electric motors.
How can thermistors improve the reliability of electric motors in various applications?
Thermistors play a vital role in enhancing the reliability of electric motors by providing precise temperature monitoring and protection. By promptly adjusting the motor's operation based on temperature readings, thermistors can prevent overheating, thus ensuring optimal performance and longevity in various applications. The integration of thermistor technology allows for more efficient and safe operation of electric motors across different industries.
How do thermistors impact the performance and lifespan of electric motors in different operational environments?
Thermistors play a crucial role in monitoring temperature and preventing overheating in electric motors, which significantly impacts their performance and lifespan. By accurately sensing temperature changes, thermistors can trigger protections against thermal damage, ensuring optimal operation across various environments. This technology helps maintain efficiency and reliability by preventing failure due to excessive heat.
How do thermistors affect the performance of electric motors in extreme environments?
Thermistors can significantly impact the performance of electric motors in extreme environments by providing accurate temperature monitoring and protection. In these situations, thermistor technology helps ensure that the motors operate within safe temperature limits, thereby enhancing their reliability and lifespan.
What are the different types of thermistors used in electric motor applications?
In electric motor applications, various types of thermistors are utilized, including positive temperature coefficient (PTC) and negative temperature coefficient (NTC) thermistors. These thermistors serve crucial roles in monitoring temperature and providing feedback to control systems, enhancing overall reliability and efficiency while extending the lifespan of electric motors.