Single-Phase vs Three-Phase Motors
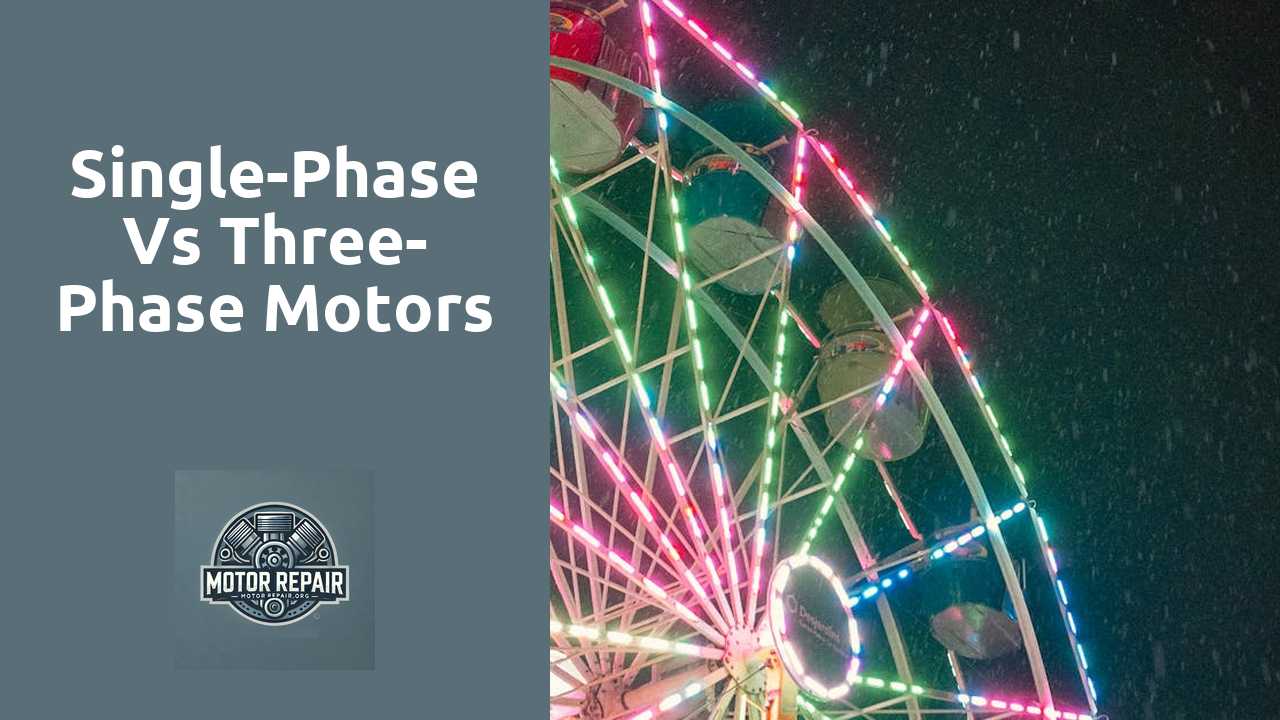
Table Of Contents
Starting Mechanisms
Starting mechanisms are crucial in determining how effectively motors initiate operation. Single-phase motors typically rely on auxiliary windings or capacitors to create the necessary phase shift for starting. Common types include the split-phase motor and the capacitor-start motor, which facilitate the creation of a rotating magnetic field. This initial movement allows the motor to overcome inertia when starting from a complete stop.
In contrast, three-phase motors utilize a more straightforward approach to starting. They can generate a rotating magnetic field automatically due to the three different phases of electrical supply. The inherent balance of the three-phase system provides a smooth and efficient start-up without additional starting mechanisms. This efficiency leads to less wear on components and reduced energy consumption during the starting phase, making them ideal for larger applications where reliability is paramount.
Navigate to these guys for detailed information.
Starting Methods for Single-Phase Motors
Single-phase motors typically require additional components to start effectively. One common method involves using a start capacitor, which stores electrical energy and releases it to create a phase shift. This phase shift helps establish the necessary rotating magnetic field for the motor to begin turning. Once the motor reaches a specific speed, a centrifugal switch disconnects the capacitor, allowing the motor to run on its main winding.
Another approach employs a shaded pole motor design, which utilizes a portion of the stator coil that is slightly shaded from the magnetic field. This creates a phase difference between the windings, enabling the motor to start. These motors are relatively simple and cost-effective, making them suitable for small applications like fans and small pumps. However, their efficiency is lower than that of capacitor-start motors, and they are often limited to lighter loads.
Starting Methods for Three-Phase Motors
Three-phase motors typically utilize several effective starting methods to ensure smooth operation and minimize stress on the electrical components. The direct-on-line (DOL) starter is one of the most common techniques, providing full voltage directly to the motor at startup. This method is straightforward and cost-effective but may cause high starting currents, potentially leading to voltage drops in the supply network.
Another widely used starting method is the star-delta starter, which initially connects the motor windings in a star configuration to reduce the voltage during startup. After reaching a certain speed, the motor switches to delta configuration for normal operation, allowing for a lower starting current. This technique not only protects the motor itself but also reduces the strain on electrical systems, making it an efficient choice for larger motors in industrial settings.
Techniques for Efficient Operation
Understanding the specific demands of the application can greatly enhance the efficiency of motor operation. Correct sizing is crucial; an oversized or undersized motor can lead to energy losses and reduce operational effectiveness. Regular maintenance, including lubrication and cleaning, plays a significant role in ensuring the longevity and smooth functioning of the motor. Moreover, incorporating smart controls or variable frequency drives can optimize energy consumption by adjusting the motor speed to match the load requirements.
Monitoring temperature and vibrations can help in early detection of potential issues. Excessive heat often indicates inefficiencies or mechanical problems that could lead to motor failure. Implementing regular inspections can prevent unexpected downtime and costly repairs. Using appropriate power supply configurations also contributes to improved efficiency, particularly in three-phase systems where balanced loads minimize losses and enhance performance. Adhering to best practices in operation and maintenance is essential for achieving optimal results from any motor system.
Installation Considerations
When installing motors, proper planning and assessment of the installation environment are crucial. Considerations such as voltage requirements, ambient temperature, and available space will significantly affect motor performance. For single-phase motors, it is essential to ensure that the circuit can adequately support the starting current, as inadequate wiring can lead to overheating or premature failure. Meanwhile, three-phase motors typically require compatible power sources, and ensuring alignment with the system’s specifications promotes efficiency.
Positioning also plays a pivotal role in installation. Adequate ventilation must be ensured to prevent overheating, especially in enclosed spaces. Both types of motors should have sufficient clearance to allow for maintenance and avoid obstructing airflow. Accessibility for servicing is equally important in minimizing downtime and facilitating repairs. Additionally, grounding the motor correctly is vital for safety and to mitigate electrical hazards during operation.
Factors to Consider When Installing Motors
Proper installation of motors is crucial for optimal performance and longevity. Selection of the right motor type for specific applications can significantly impact efficiency. Protective enclosures must meet environmental demands, ensuring durability in different settings. Furthermore, adhering to electrical standards and safety codes minimizes risks during operation.
Additionally, sufficient space for airflow is vital to prevent overheating. Alignment with the driven equipment should be precise to reduce wear on components. Vibration and noise levels should be monitored to enhance operational comfort. Proper grounding practices are essential to avoid electrical hazards and enhance system reliability.
FAQS
What is the main difference between single-phase and three-phase motors?
The main difference lies in the number of power supply phases. Single-phase motors operate on a single alternating current (AC) phase, while three-phase motors use three AC phases, providing a more consistent and efficient power supply.
Which type of motor is more efficient, single-phase or three-phase?
Three-phase motors are generally more efficient than single-phase motors. They can handle higher loads with less energy loss and provide smoother operation, making them more suitable for industrial applications.
What are common applications for single-phase motors?
Single-phase motors are commonly used in residential and light commercial applications, such as small appliances, fans, and pumps where lower power and efficiency are sufficient.
Can a single-phase motor be converted to a three-phase motor?
While it is technically possible to convert a single-phase motor to a three-phase motor through the use of variable frequency drives (VFDs) or phase converters, it is often more practical to simply replace it with a three-phase motor if three-phase power is available.
What factors should I consider when installing a motor?
Key factors to consider include the power supply available (single-phase vs three-phase), motor size and type, load requirements, environmental conditions, and alignment with existing machinery or equipment to ensure optimal performance.
Related Links
industrial motor repairBrushless DC Motors: Advantages and Disadvantages
Servo Motors in Industrial Automation
Permanent Magnet Motors: Types and Features