Servo Motors in Industrial Automation
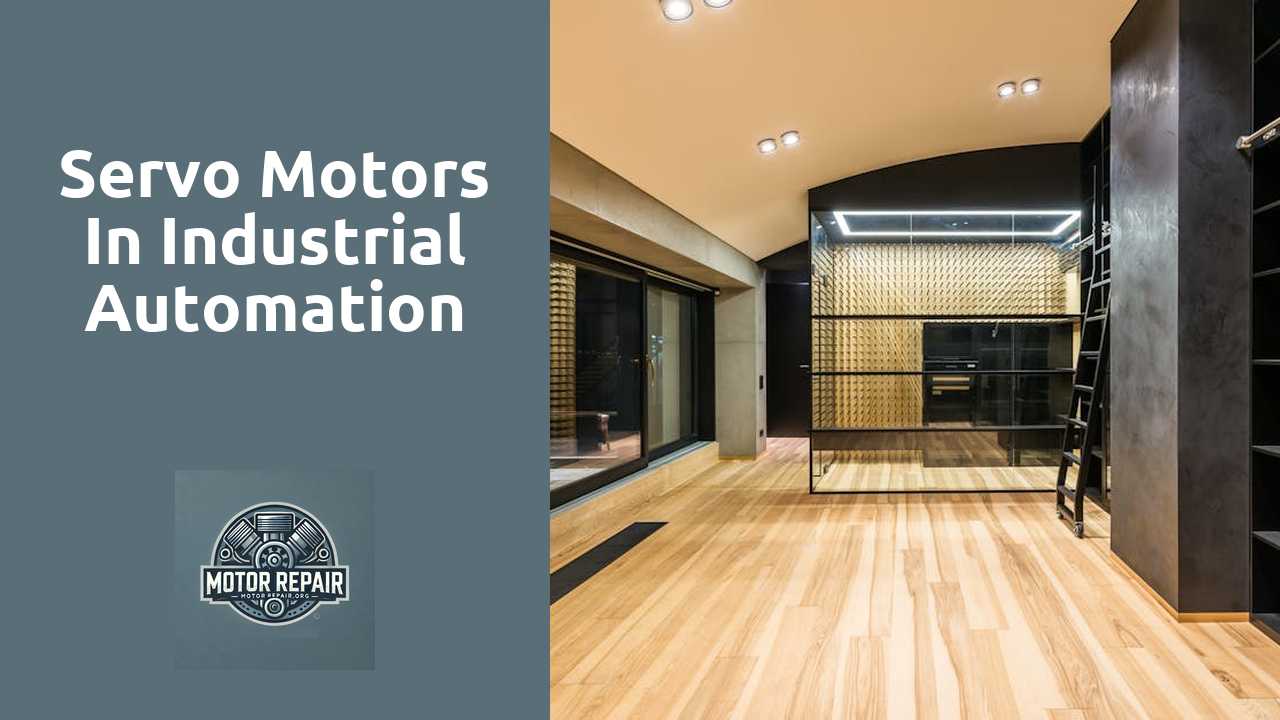
Table Of Contents
Installation Best Practices
Proper installation of servo motors is crucial for optimal performance and longevity. Begin by ensuring that the mounting surface is clean and stable. Any vibrations or misalignments can lead to operational inefficiencies. Alignment of the motor shaft with the driven load should be precise, as misalignment can cause excessive wear or motor failure. Additionally, when selecting mounting hardware, it is important to use appropriate materials that can withstand the operational environment and mechanical stress.
Wiring should be conducted with care, adhering to manufacturer specifications. This includes correctly identifying signal and power connections, which can significantly influence performance. Employ shielded cables to minimize noise interference, particularly in areas with significant electromagnetic activity. After installation, comprehensive testing is essential. This includes verifying all connections and conducting a series of performance tests to ensure the motor operates within defined parameters. Regular maintenance checks will also help to identify any potential issues before they escalate.
View this external resource for great tips and advice.
Steps for Proper Setup and Calibration
Proper setup and calibration of servo motors is critical for optimal performance. Initially, one must ensure that the mounting of the motor aligns precisely with its corresponding load. This requires checking the shaft alignment to prevent undue stress and wear. Secure all mounting bolts to the recommended torque specifications and verify that the coupling is well-fitted. Complications during installation can lead to diminished performance, necessitating meticulous attention to details.
After the physical installation, configuring the motor parameters is essential. It is advisable to reference the manufacturer's guidelines for setting the controller parameters. Adjustments to gain settings and feedback loops may be necessary to fine-tune the system response. Following these initial settings, conducting a series of tests will aid in determining whether the motor reacts as expected under load conditions. Continually monitoring performance metrics can assist in identifying areas needing further calibration.
Common Issues and Troubleshooting
Servo motors, while highly efficient and reliable, can encounter several common issues that may hinder their performance in an industrial environment. Overheating is a frequently reported problem, often caused by excessive load, inadequate cooling, or increased friction in the motor components. Regular checks of the motor's temperature and ensuring that cooling systems are operational can help mitigate this issue. Additionally, incorrect wiring or connection issues can lead to erratic behavior or failure in responsiveness. It is crucial to inspect all electrical connections and ensure wiring conforms to the manufacturer's specifications.
Another common complication involves poor feedback from the servo motor, which can result in inaccurate positioning or oscillation. This can stem from misconfigured controllers or sensors that fail to communicate properly with the motor. Regular calibration of the feedback system is essential to maintain accuracy. Voltage fluctuations may also disrupt performance; implementing voltage stabilizers can help maintain consistency. Diagnosing these issues often requires systematic troubleshooting to identify the root causes and restore optimal function.
Identifying and Resolving Performance Problems
Servo motors can exhibit various performance issues that hinder their efficiency and effectiveness in industrial automation settings. Common problems include vibrations, excessive heat generation, and response delays. These symptoms can be linked to several factors, including misalignment, incorrect tuning of control parameters, or electrical supply issues. By closely monitoring the motor's behavior and using diagnostic tools, operators can pinpoint the underlying causes of these performance anomalies.
To address these issues, a systematic approach is essential. Start with ensuring that the motor is correctly installed and well-aligned with its load. Review the control settings and make necessary adjustments to the PID parameters to optimize feedback control. Regular maintenance checks, such as inspecting wiring and connectors, are crucial in preventing or identifying electrical faults early on. Implementing these practices helps in restoring and maintaining the desired performance levels of servo motors in an industrial environment.
Advances in Servo Motor Technology
Recent innovations have significantly enhanced the performance of servo motors, particularly through improvements in control algorithms. These advancements allow for more precise movement and increased speed, resulting in higher efficiency for industrial applications. Enhanced feedback systems, such as encoder technology, provide accurate position data, enabling servo motors to execute complex tasks with greater reliability. New materials and manufacturing techniques have also contributed to lighter and more powerful motor designs, further optimizing their performance in diverse settings.
The integration of IoT technology has transformed the way servo motors are utilized in automation. With real-time data monitoring capabilities, operators can track performance metrics and detect potential issues before they escalate into serious problems. This connectivity allows for remote diagnostics and updates, reducing downtime and maintenance costs. Consequently, industries can benefit from improved adaptability, as servo motors equipped with smart features can be seamlessly integrated into existing systems to enhance overall productivity.
The Impact of IoT on Automation
The integration of the Internet of Things (IoT) with industrial automation has transformed the way servo motors operate within manufacturing environments. By leveraging IoT technology, organizations can collect real-time data from servo motors and other machinery. This data can then be analyzed to optimize performance, predict maintenance needs, and reduce downtime. Enhanced monitoring capabilities allow for a more responsive approach to system management, enabling operators to make informed decisions based on actual machine conditions rather than on historical data alone.
Furthermore, the connectivity offered by IoT enables seamless communication between devices and centralized control systems. This interconnectedness enhances the flexibility of automation systems, allowing for swift adjustments to production processes. Machine learning algorithms can now utilize the vast amounts of data generated to improve operational efficiency and support automation strategies. Such advancements not only streamline manufacturing but also foster an environment where innovation can thrive through continuous improvement and adaptation.
FAQS
What are servo motors, and how do they work in industrial automation?
Servo motors are specialized motors designed for precise control of angular position, velocity, and acceleration. In industrial automation, they are used in applications requiring high accuracy and responsiveness, such as robotics, conveyor systems, and CNC machines.
What are some best practices for installing servo motors?
Best practices for installing servo motors include ensuring proper alignment with load mechanisms, securing all connections, using suitable mounting hardware, and following the manufacturer's guidelines for wiring and configuration to prevent misalignment and electrical issues.
What common issues can arise with servo motors in industrial applications?
Common issues with servo motors include overheating, loss of feedback signals, mechanical binding, and incorrect calibration. These problems can lead to reduced performance and require troubleshooting to resolve.
How can I troubleshoot performance problems with servo motors?
To troubleshoot performance problems, start by checking for error codes, inspecting electrical connections, and verifying the integrity of the feedback devices. Additionally, review the calibration settings and ensure that the motor is free from mechanical obstructions.
What are the latest advancements in servo motor technology?
Recent advancements in servo motor technology include improved energy efficiency, enhanced control algorithms, and integration with IoT systems for real-time monitoring and predictive maintenance, which help optimize performance and reduce downtime in industrial automation systems.
Related Links
industrial motor repairBrushless DC Motors: Advantages and Disadvantages
Single-Phase vs Three-Phase Motors
Permanent Magnet Motors: Types and Features