What are the common faults in a DC motor?
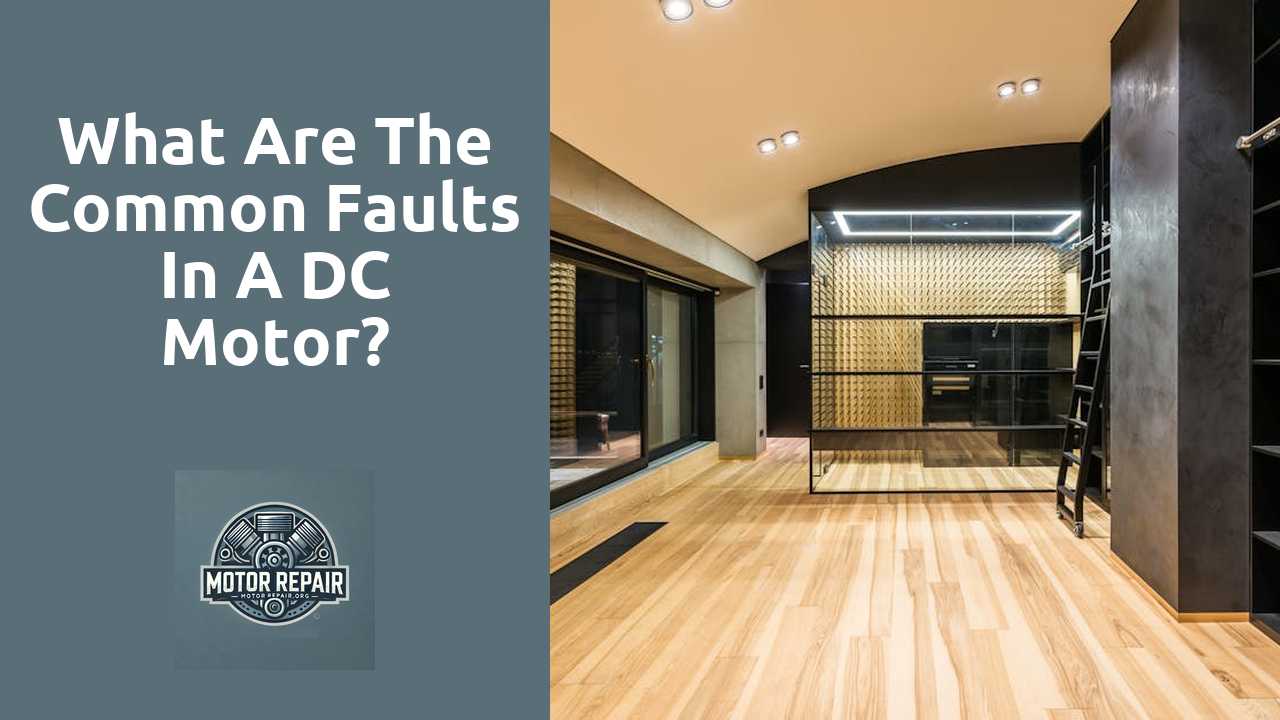
Table Of Contents
Brushes Problems in DC Motors
DC motors rely on brushes to ensure proper electrical contact with the commutator, and issues with brushes can lead to significant performance problems. Worn brushes may result in inconsistent connectivity, causing fluctuations in speed and torque. The material and quality of the brushes impact their lifespan, often resulting in varied wear patterns that exacerbate operational inefficiencies.
Another common issue involves poor contact between the brushes and the commutator. This can be due to improper seating or misalignment, leading to increased friction and heat generation. Insufficient contact can also result in sparking, which damages both the brushes and the commutator over time. Regular maintenance and timely replacement of brushes are essential to mitigate these issues and maintain optimal performance in DC motors.
Here is a super informative post that goes into more detail.
Brush Wear and Contact Issues
Brush wear is a common issue in DC motors that can significantly affect performance. As brushes make contact with the commutator, they experience friction, leading to gradual erosion over time. This wear can result in insufficient contact, causing inconsistent electrical conductance. Consequently, the motor may experience reduced efficiency and power output. The type of material used for brushes can influence the rate of wear. Softer materials may wear down faster but can provide a smoother operation initially.
Maintaining proper contact between brushes and commutators is crucial for optimal motor function. Deterioration of the contact surface can lead to sparking and increased heat generation. This not only affects the longevity of the brushes but can also result in damage to the commutator itself. Regular inspection and maintenance of brush condition can help minimize these issues, ensuring that the motor operates smoothly and reliably.
Overheating Causes
Excessive load is one major contributor to overheating in DC motors. When a motor is subjected to loads beyond its rated capacity, it forces the motor to work harder than intended. This increased effort leads to a rise in temperature, which can cause damage to insulation and reduce the overall lifespan of the motor. Continuous operation under such conditions can ultimately result in failure of the motor components.
Another factor that can lead to overheating is inadequate ventilation. Proper cooling is crucial for maintaining optimal operating temperatures. If a motor is housed in an environment that restricts airflow or if cooling fans are malfunctioning, the heat generated during operation may not dissipate efficiently. This accumulation of heat can escalate to critical levels, affecting performance and potentially causing irreversible harm to the motor's internal systems.
Impact of Excessive Load
Excessive load on a DC motor can lead to significant operational issues. When the motor is subjected to a demand beyond its rated capacity, it struggles to maintain its performance levels, often resulting in a stall condition. This not only affects the motor’s efficiency but also puts additional strain on connected components, potentially leading to mechanical failure and costly downtime.
As the load increases beyond normal limits, overheating becomes a critical concern. The higher current draw required to sustain operation can overheat the windings and other internal parts. Prolonged exposure to such conditions may degrade insulation and ultimately shorten the lifespan of the motor. Monitoring performance metrics is essential to prevent operational issues related to excessive loads.
Performance Impacts of Vibration
Vibration can significantly influence the overall efficiency and lifespan of a DC motor. When a motor experiences excessive vibration, it can lead to premature wear of components, such as bearings and rotor windings. This wear can compromise the motor's performance, leading to increased maintenance costs and potential downtimes. Furthermore, vibrations can create misalignment issues within the motor's structure. Misalignment can exacerbate existing mechanical problems, resulting in a cascading effect on the motor's stability and operational capabilities.
The presence of vibration might also affect the accuracy of feedback systems utilized for control purposes. Sensors that provide crucial data for performance monitoring can become less reliable when subjected to vibrations. Erratic readings from these sensors can lead to incorrect adjustments in operational parameters. This inconsistency not only affects efficiency but can also create safety concerns when motors operate under uncontrolled conditions. Addressing vibration issues promptly is essential for maintaining optimal performance in DC motors.
Identifying Sources of Vibration
Vibration in a DC motor can arise from various mechanical and electrical factors. Misalignment of components often leads to additional stress on the motor, causing it to vibrate excessively during operation. Bearings that are worn out or improperly lubricated may also generate vibrations due to increased friction. Furthermore, imbalance in rotor assemblies can create uneven forces, exacerbating the issue and resulting in a noisy operation.
Another possible source of vibration is electrical imbalance stemming from inconsistent power supply. Fluctuations in the voltage or inconsistencies in the current can affect the performance of the motor. Loose connections or faulty wiring can further contribute to fluctuations, making the motor susceptible to vibration. Regular maintenance and monitoring of both mechanical and electrical components are essential to identify these potential vibration sources effectively.
FAQS
What are the common faults in a DC motor?
Common faults in a DC motor include brush wear and contact issues, overheating due to excessive load, and performance impacts caused by vibration.
How can brush wear affect the performance of a DC motor?
Brush wear can lead to poor electrical contact, resulting in increased resistance, reduced efficiency, and potential motor failure due to inconsistent power delivery.
What causes overheating in a DC motor?
Overheating in a DC motor is often caused by excessive load, poor ventilation, or insufficient cooling, which can damage the motor's windings and insulation.
How can I identify vibration problems in my DC motor?
Vibration problems can be identified through visual inspection for loose components, unusual noise, or using vibration analysis tools to detect abnormal patterns.
What maintenance practices can help prevent common faults in a DC motor?
Regular maintenance practices such as inspecting and replacing brushes, ensuring proper alignment, monitoring load conditions, and maintaining adequate cooling can help prevent common faults in a DC motor.
Related Links
dc electric motor repairIs it worth repairing an electric motor?
Can a DC motor be repaired?
What is the life expectancy of a DC motor?