How is motor winding done?
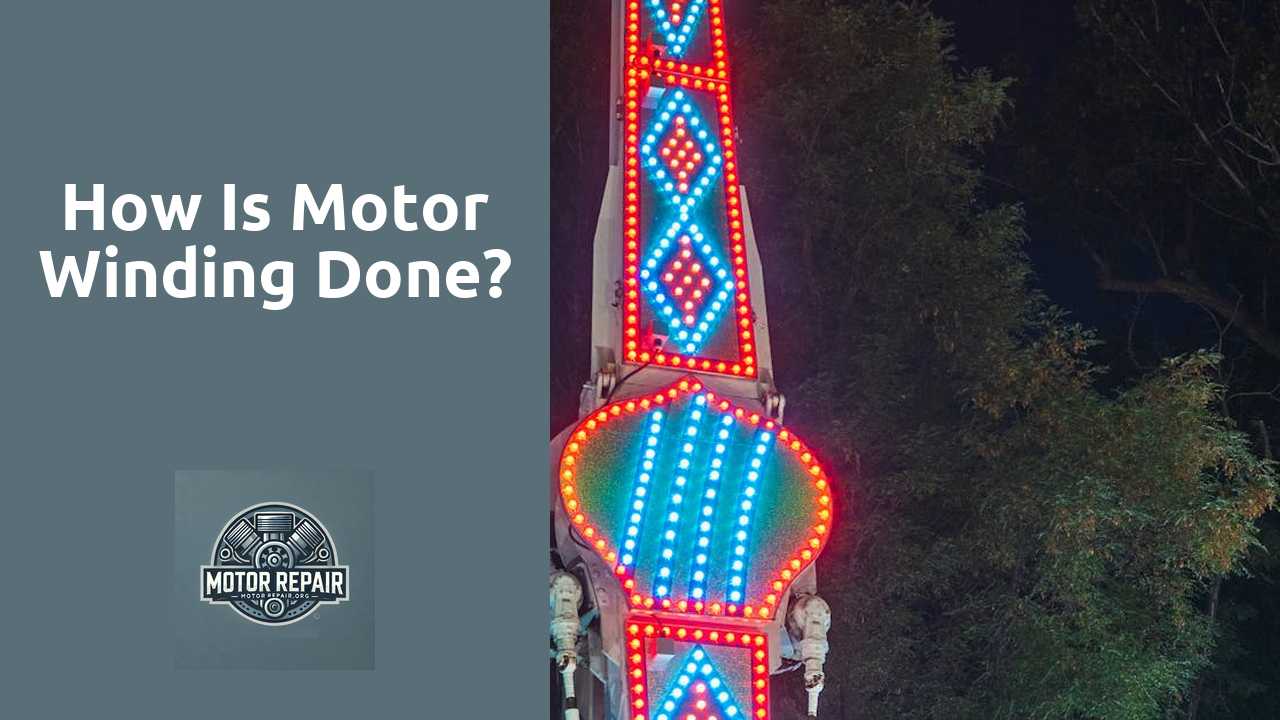
Table Of Contents
Common Techniques in Motor Winding
Motor winding is an intricate process with several techniques employed to achieve optimal efficiency and durability. One commonly used method is the lap winding technique, which provides low voltage and high-current applications. This approach involves winding the coils in a staggered manner, allowing for even distribution of the windings across the core. Another popular technique is the wave winding method. This creates a wave-like formation that results in higher voltage and is often used in generators and other applications where increased efficiency is required.
In addition to these traditional methods, advancements in technology have led to the introduction of automated winding systems. These systems are designed to enhance precision and reduce human error, significantly improving production speed. Programmable machines can execute complex winding patterns consistently, ensuring uniformity in each component produced. While automation brings efficiency, manual winding remains important for specialized applications where craftsmanship and attention to detail are crucial.
Continue reading this article for more information.
Manual vs. Automated Winding
Manual winding is a traditional technique that has been employed for years. It involves skilled operators who meticulously wind the coils around the motor's stator and rotor. This method allows for precise control over the winding process and can be particularly advantageous for custom motors or specialized applications. The expertise of the technician plays a crucial role in ensuring that the wire is evenly distributed and that the coil is formed correctly.
In contrast, automated winding utilizes specialized machines programmed to execute the winding process with high precision. These machines can significantly increase production efficiency and reduce human error. The consistency achieved through automation is particularly beneficial in large-scale manufacturing settings, where uniformity is essential. Although automation may lack the nuanced touch of a skilled craftsman, advancements in technology have made machines capable of producing high-quality windings that meet stringent specifications.
Testing and Quality Control in Winding
Ensuring the reliability and performance of motor windings necessitates rigorous testing and quality control measures. Various methods are employed to verify the integrity of the winding wire, including insulation resistance tests and continuity checks. These assessments help detect potential faults in the winding that could compromise motor function. Additionally, visual inspections are critical to identify any inconsistencies in winding patterns or material defects that may affect performance.
Quality control procedures often involve both in-process and final inspections to uphold manufacturing standards. Automated systems may integrate real-time monitoring to track winding parameters, while manual inspections provide opportunities to catch issues that machines might overlook. By adhering to these stringent testing protocols, manufacturers can ensure that every assembled motor meets the specifications required for optimal operation and longevity.
Methods to Ensure Proper Functionality
Ensuring proper functionality in motor windings requires meticulous attention to detail throughout the winding process. One critical method involves selecting the right insulation materials between the winding turns. High-quality insulation prevents electrical shorts and contributes to the motor's thermal stability. Additionally, maintaining the correct tension while winding ensures uniformity and prevents excess wear on winding components. Consistency in these factors greatly enhances the longevity and performance of the motor.
Another essential method is the implementation of electrical testing after the winding is complete. This includes resistance testing to ensure that the resistance falls within acceptable limits. Any discrepancies in resistance readings can indicate potential short circuits or faulty connections. Furthermore, using advanced diagnostic tools can help in assessing the integrity of the winding. Regular assessments can identify early signs of wear or damage, allowing for preventative measures before the motors are deployed in operational settings.
Troubleshooting Common Winding Issues
In motor winding, various issues may arise that can impact performance. Identifying these problems early is crucial. Signs of winding faults can include unusual noises, overheating, or poor electrical performance. A common issue is shorted turns, where adjacent wire turns make contact, resulting in reduced efficiency. This can often be diagnosed through impedance testing, where a drop in expected resistance indicates a problem within the coil.
Another frequent challenge involves open circuits in the winding. Such faults occur when the wire breaks, disrupting the electrical current flow. Using a multimeter to check continuity can help detect open circuits. Additionally, proper insulation during the winding process is vital. Deterioration in insulation can lead to leakage currents, further complicating performance issues. Ensuring integrity in materials from the start can greatly reduce these risks.
Identifying and Fixing Faults
When working with motor windings, pinpointing faults is crucial for maintaining optimal performance. Common issues include short circuits, open circuits, and insulation failures. Visual inspection is often the first step in identifying these problems. Winding turns may be inspected for signs of damage, burn marks, or unusual wear. Using a multimeter can help measure resistance and continuity, revealing whether the winding paths are intact or if there are breaks in the circuit.
Once faults are identified, addressing them typically involves a systematic approach. For short circuits, isolating the affected winding turns or sections may be necessary. Open circuits can often be repaired by replacing damaged wire or reconnecting broken strands. It’s essential to ensure that insulation is restored properly to prevent further issues. Regular maintenance checks help catch these problems early, reducing potential downtime and ensuring the efficient operation of the motor.
FAQS
What is motor winding?
Motor winding refers to the process of creating coils of wire that generate a magnetic field when electric current passes through them, which is essential for the operation of electric motors.
What are the common techniques used in motor winding?
Common techniques in motor winding include manual winding, automated winding, and the use of specialized machinery to ensure precision and efficiency in the winding process.
How does manual winding differ from automated winding?
Manual winding involves skilled technicians hand-winding the coils, allowing for more control and customization, while automated winding uses machines to perform the winding process quickly and consistently, improving production efficiency.
What methods are used for testing and quality control in winding?
Testing and quality control methods may include electrical testing, visual inspections, insulation resistance tests, and performance checks to ensure that the windings meet required specifications and functionality.
What are some common winding issues and how can they be troubleshot?
Common winding issues include shorts, breaks, and uneven winding. Troubleshooting these problems involves identifying the fault through visual inspection, testing for continuity, and repairing or rewinding the affected sections as needed.
Related Links
motor rewindingIs rewinding a motor worth it?
Is it cheaper to rewind a motor or buy a new one?
What is the cost of rewinding a motor?